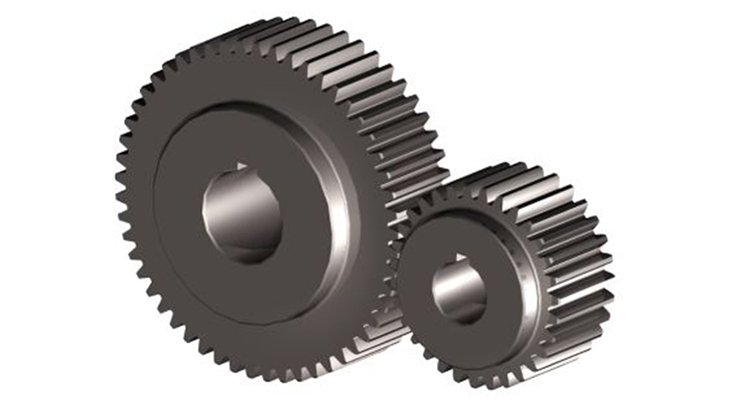
Spur Gear
Features of Spur Gears
Spur gears are one of the most common types of gears and are widely used in variousapplications such as machinery, automotive, and industrial equipment. The main features and uses of spur gears are:
1.Transmitting power: Spur gears are used to transmit power and motionbetween two parallel shafts. The teeth of the gears mesh with each other to transfer rotational force and torque.
2.Straight teeth: Spur gears have straight teeth that run parallel to the axis of rotation, which makes them simple and easy to manufacture.
3.Efficiency: Spur gears have high efficiency due to their low-friction meshing, which helps to minimize power loss and heat generation.
4.Speed reduction or increase: Spur gears can be used to reduce or increase thespeed of the output shaft relative to the input shaft, depending on the number of teeth on each gear.
5.Noise: Spur gears can produce noise and vibration due to the straight cut teethmeshing, which can be reduced by using noise reduction techniques like helical gears.
6.Durability: Spur gears are durable and can handle high loads and speeds, but they can wear out quickly if not lubricated properly.
7.Size and shape: Spur gears come in different sizes and shapes, ranging fromsmall gears used in watches to large gears used in heavy machinery.
Overall, spur gears are versatile and reliable components that are widely used in variousapplications due to their simplicity, efficiency, and durability
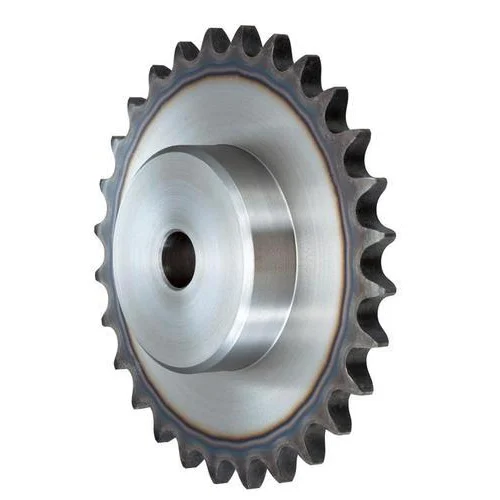
Sprocket Gear
Sprocket gears are a type of gear used in chain drives to transfer rotational motion fromone shaft to another. They have teeth that mesh with the links of a chain, providing a positive engagement and a smooth, continuous transfer of power. In this blog post, wewill explore the advantages and applications of sprocket gears.
Advantages of Sprocket Gears
Applications of Sprocket Gears
Conclusion
Sprocket gears are a versatile and efficient type of gear system that is essential for chaindrives. With their high efficiency, reliable operation, simple design, and versatility, sprocket gears are suitable for a wide range of applications, including bicycles, motorcycles, industrial machinery, and agricultural equipment. Sprocket gears are an excellent choice for applications where a positive engagement and a smooth, continuoustransfer of power are required.
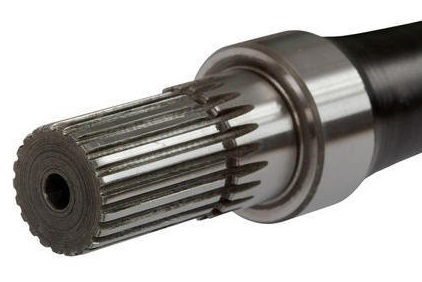
Spline Gear
Splines are mechanical devices that are used to transmit torque and power between rotating shafts and other components such as gears, couplings, and bearings. The main features and uses of splines gear are:
1.Transmitting power: Splines are used to transmit power and torque between shafts, providing a secure connection that can handle high loads and speeds.
2.Reducing stress concentration: Splines can help to reduce stress concentration in the connection between shafts by distributing the load over a larger area.
3.High precision: Splines are designed to provide a high degree of precision and accuracy, ensuring that the connection between shafts is tight and secure.
4.Easy assembly and disassembly: Splines can be easily assembled and disassembled without the need for specialized tools or equipment, making maintenance and repair easier.
5.Versatility: Splines can be used in a variety of applications, including automotive, aerospace, and industrial equipment.
6.Different types: There are several different types of splines, including involute splines, serrated splines, and crowned splines, each with its own advantages and disadvantages.
7.Efficient torque transmission: Splines are efficient at transmitting torque due to the large contact area between the shafts, which helps to minimize power loss and heat generation.
Overall, splines are an important component in many mechanical systems and provide a reliable and efficient means of transmitting power and torque between shafts. Their precision, ease of use, and versatility make them a popular choice for a wide range of applications.
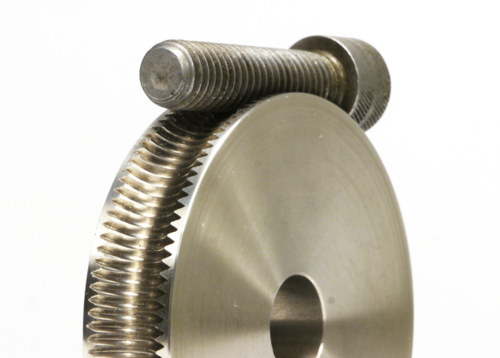
Screw Gear
Screw gears, also known as worm gears, are a type of gear system that uses a helicalscrew and a gear wheel to transmit power and motion. In this blog post, we will explorethe advantages and applications of screw gears.
Advantages of Screw Gears
Applications of Screw Gears
Conclusion
Screw gears are a versatile and reliable gear system that is ideal for a wide range of applications. With their high reduction ratios, compact size, self-locking capabilities, and low noise levels, screw gears provide an efficient and effective way to transmit power and motion. From lifting systems to industrial machinery to automotiveapplications, screw gears are a critical component in many different types of machineryand equipment.
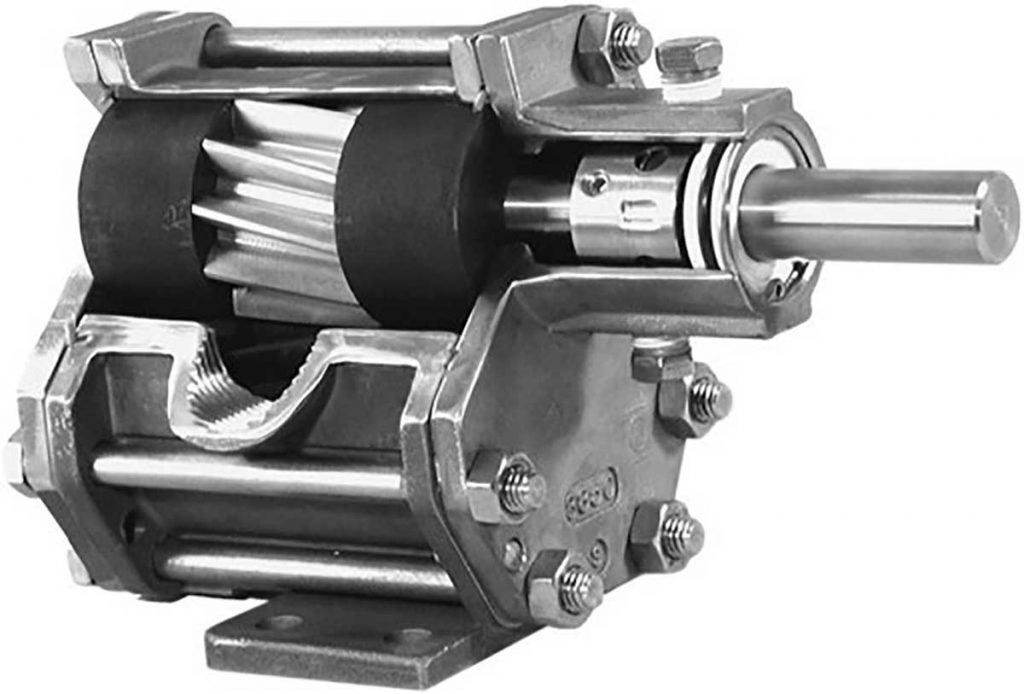
Pump Gear
Pump gear refers to the gear set used in positive displacement pumps to transfer fluidsfrom one location to another. These gear sets are essential components in manyindustries, including oil and gas, chemical processing, and food and beverage. In thisblog post, we will take a closer look at pump gear, its functions, types, and benefits.
Functions of Pump Gear
The primary function of pump gear is to transfer fluids from one location to another in a positive displacement pump. Positive displacement pumps work by trapping a fixedamount of fluid between the gears and the pump housing, and then transferring thatfluid from the inlet to the outlet. Pump gear plays a critical role in this process, ensuringthat the fluid is transferred efficiently and effectively.
Types of Pump Gear
There are several different types of pump gear available on the market, each designedfor specific applications and operating conditions. Some of the most common types of pump gear include:
Benefits of Pump Gear
Pump gear offers several benefits over other types of pump components. Some of themost significant benefits of pump gear include:
In conclusion, pump gear is an essential component in many industrial applications. It is designed to transfer fluids from one location to another efficiently and effectively, making it critical to the operation of positive displacement pumps. By understanding thefunctions, types, and benefits of pump gear, users can select the right type of gear fortheir specific application, ensuring maximum performance and efficiency.
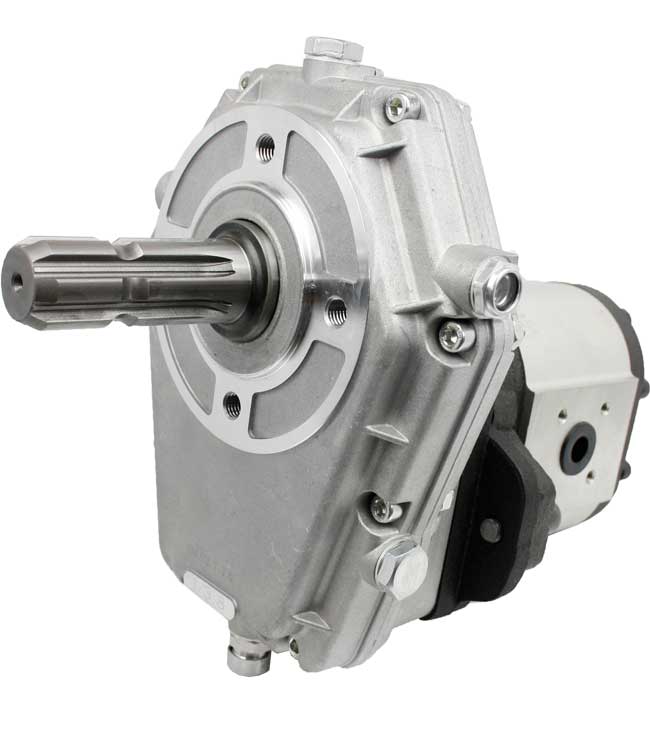
Pto Gear
A PTO (Power Take-Off) gear is a type of gear system that is used to transfer powerfrom a vehicle’s engine to other mechanical systems, such as hydraulic pumps oragricultural equipment. PTO gears are commonly found in tractors, trucks, and otherheavy machinery, and play a critical role in powering attachments and implements. Inthis blog post, we will explore the benefits and applications of PTO gears.
Advantages of PTO Gears
Applications of PTO Gears
Conclusion
PTO gears are a versatile and reliable type of gear system that is critical to poweringattachments and implements in a wide range of applications, including agriculture, construction, transportation, and industrial machinery. With their high efficiency, reliability, and versatility, PTO gears are an essential component of many mechanicalsystems. Whether used in tractors, trucks, or other heavy machinery, PTO gearsprovide operators with control over power output and help to increase productivity andefficiency.
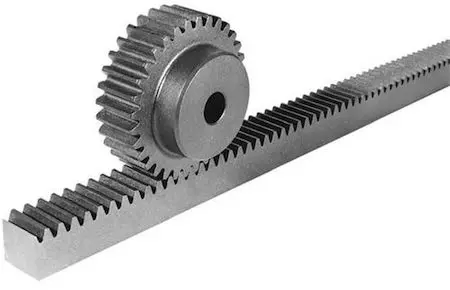
Pinion Gear
Pinion gears are a type of gear system that is used to transfer power and motion betweentwo rotating shafts. These gears are typically small and have teeth that mesh with theteeth of a larger gear, called a gear wheel or gear ring. In this blog post, we will explorethe benefits and applications of pinion gears.
Advantages of Pinion Gears
Applications of Pinion Gears
Conclusion
Pinion gears are a versatile and reliable type of gear system that can transfer power andmotion between two rotating shafts with high efficiency. These gears are often small andcompact, which makes them suitable for use in tight spaces, and they can be used in a wide range of applications, including automotive, industrial, and power transmissionsystems. With their durability and long-lasting performance, pinion gears are an essential component of many mechanical systems.
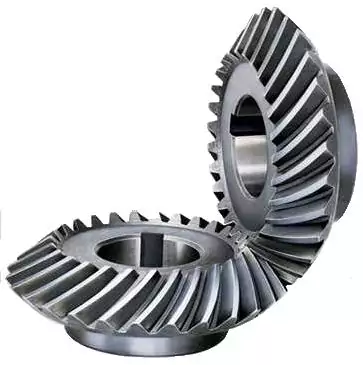
Miter Gear
Miter gears are a type of gear used to transfer rotational motion between two intersecting shafts at a right angle. They consist of two gear wheels with the samenumber of teeth, and the gears have teeth that are cut at an angle of 45 degrees to theaxis of rotation. In this blog post, we will explore the advantages and applications of miter gears.
Advantages of Miter Gears
Applications of Miter Gears
Conclusion
Miter gears are a versatile and efficient type of gear system that is essential fortransferring power at right angles. With their smooth operation, high efficiency, andspace-saving design, miter gears are suitable for a wide range of applications, includingpower transmission, printing, machine tool, automotive, and robotics industries. Mitergears are an excellent choice for applications with limited space, where a right angletransfer of power is required.

Internal Gear
Internal gears are a type of gear system that is designed with teeth on the inside of thegear, rather than on the outside. These gears are often used in mechanical powertransmissions to achieve high gear reduction ratios and transmit torque in a compactspace. In this blog post, we will explore the benefits and applications of internal gears.
Advantages of Internal Gears
Applications of Internal Gears
Conclusion
Internal gears are a versatile and reliable type of gear system that can achieve high gearreduction ratios and transmit torque in a compact space. These features make themsuitable for a wide range of applications, including wind turbines, robotics, printingpresses, and industrial machinery. With their smooth operation, high load capacity, andreliable performance, internal gears are an essential component of many mechanicalsystems.
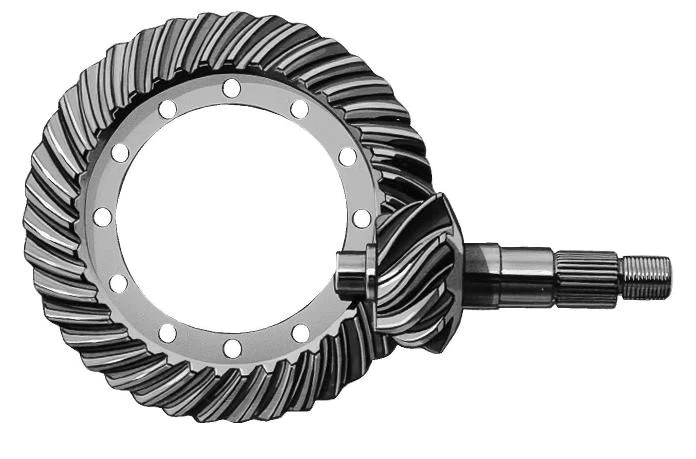
Hypoid Gears
Hypoid gears are a type of gear used to transfer rotational motion between two intersecting shafts that are not parallel. They have a unique tooth profile that combinesthe features of spiral bevel gears and worm gears, making them suitable for a widerange of applications. In this blog post, we will explore the advantages and applicationsof hypoid gears.
Advantages of Hypoid Gears
Applications of Hypoid Gears
Conclusion
Hypoid gears are a versatile and efficient type of gear system that is essential fortransferring power between two intersecting shafts that are not parallel. With their highefficiency, quiet operation, and increased torque, hypoid gears are suitable for a widerange of applications, including automotive, industrial, aerospace, and roboticsindustries. Hypoid gears are an excellent choice for applications where high torque andsmooth operation are required.