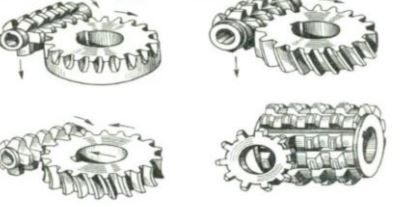
Gear Manufacturing Processes: From Design to Production
Gears are essential components used in various industries, from automotive and aerospace to machinery and robotics. The manufacturing of gears requires a precise and systematic approach to ensure optimal performance, durability, and reliability. In this blog post, we will explore the key steps involved in gear manufacturing processes, from design to production.
Gear Design:
The first step in gear manufacturing is the design phase. Gear designers utilize specialized software and tools to create the gear geometry, taking into account factors such as tooth profile, module, pressure angle, and pitch diameter. The design process also involves considering the specific application requirements, load capacity, and desired performance characteristics of the gear.
Material Selection:
Choosing the right material for gear production is crucial to ensure strength, wear resistance, and durability. Commonly used materials for gears include alloy steels, stainless steels, and non-ferrous metals like bronze and brass. The material selection is based on factors such as load capacity, operating conditions, and cost considerations.
Gear Cutting:
Gear cutting is a critical process in gear manufacturing. It involves removing material from a gear blank to create the desired tooth profile. There are several methods for gear cutting, including hobbing, shaping, milling, and broaching. Each method has its advantages and is chosen based on factors such as gear type, volume, and accuracy requirements.
Heat Treatment:
After gear cutting, the gears often undergo heat treatment processes to enhance their mechanical properties. Heat treatment techniques such as carburizing, quenching, and tempering are employed to achieve desired hardness, toughness, and wear resistance. Heat treatment ensures that the gears can withstand the stresses and loads they will encounter during operation.
Finishing Operations:
Once the gears have undergone heat treatment, they go through various finishing operations. These include grinding, honing, lapping, and deburring to achieve the desired surface finish, dimensional accuracy, and tooth profile quality. Finishing operations are essential for reducing noise, improving gear meshing, and ensuring smooth and efficient operation.
Inspection and Quality Control:
Throughout the manufacturing process, gears undergo rigorous inspection and quality control measures. This involves using precision measurement tools and equipment to check dimensional accuracy, tooth profile, surface finish, and hardness. Advanced inspection techniques such as coordinate measuring machines (CMMs) and non-destructive testing methods are employed to ensure the gears meet the required specifications and standards.
Assembly and Testing:
In some applications, gears are assembled into gearboxes or transmission systems. This involves carefully aligning the gears, shafts, and bearings to ensure proper gear meshing and smooth operation. Gear assemblies are then subjected to functional testing, including load testing, noise testing, and endurance testing, to verify their performance under real-world conditions.
Gear manufacturing is a complex and precise process that involves multiple steps, from gear design to production. Each step, from gear cutting and heat treatment to finishing operations and quality control, is crucial in ensuring the final gears meet the required specifications and performance standards. By following a systematic approach and employing advanced manufacturing techniques, gear manufacturers can produce high-quality gears that provide reliable and efficient performance in various applications.