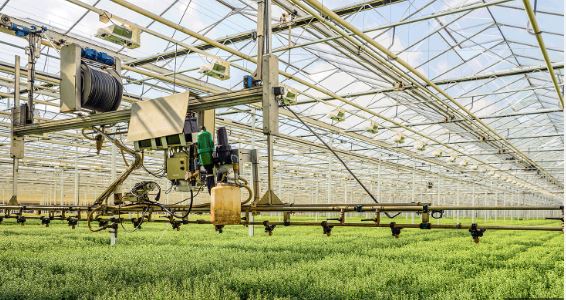
The Role of Gears and Gearboxes in Livestock Equipment and Greenhouse Automation
Livestock equipment and greenhouse automation systems play a crucial role in modern agriculture. Within these applications, gears and gearboxes are essential components that enable precise control, motion transmission, and automation. Gears facilitate power transmission and motion control, while gearboxes provide speed adjustment and torque conversion. In this blog post, we will explore the significance of gears and gearboxes in livestock equipment and greenhouse automation.
1. Livestock Equipment: a. Feed Mixers: Feed mixers are used to blend and distribute animal feed. Gears and gearboxes are employed in these machines to facilitate the mixing and distribution processes. They ensure the efficient rotation and movement of mixing blades or augers, allowing for thorough and consistent mixing of feed ingredients. b. Milking Machines: Milking machines used in dairy operations rely on gears and gearboxes for the operation of vacuum pumps and pulsators. These components facilitate the controlled suction and release of milk from he udders, ensuring efficient and hygienic milking processes.
2. Greenhouse Automation: a. Curtain Systems: Greenhouses often utilize curtain systems for environmental control. Gears and gearboxes are utilized to open and close these curtains, allowing for proper ventilation and temperature regulation. Gearboxes enable precise control over the curtain movement, ensuring optimal growing conditions for plants. b. Ventilation Systems: Gears and gearboxes play a role in automating greenhouse ventilation systems. They control the opening and closing of vents or louvers, enabling the regulation of airflow and temperature inside the greenhouse. Gearboxes offer speed adjustment, allowing for fine-tuning of ventilation rates based on environmental conditions.
3. Poultry Equipment: a. Egg Collection Systems: In poultry farms, automated egg collection systems rely on gears and gearboxes. They facilitate the movement of conveyor belts or trays, guiding eggs from the nests to collection points. Gears and gearboxes ensure smooth and reliable transportation of eggs, optimizing efficiency in egg production. b. Poultry Feeding Systems: Poultry feeding systems often utilize gear and gearbox mechanisms to regulate the distribution of feed. They control the movement of feed dispensers, ensuring accurate and timely delivery of feed to poultry. Gearboxes offer speed adjustment, allowing for precise control over feed distribution rates.
4. Durability and Reliability: Gears and gearboxes used in livestock equipment and greenhouse automation are designed to withstand challenging operating conditions. They are constructed with durable materials and precise engineering to ensure reliability and longevity. Regular maintenance and lubrication of gears and gearboxes are crucial to minimize wear and tear, ensuring optimal performance and maximizing the lifespan of these systems.
Gears and gearboxes play a vital role in livestock equipment and greenhouse automation, enabling precise control, motion transmission, and automation. Whether it’s feed mixers, milking machines, greenhouse curtain systems, or poultry equipment, these components contribute to the efficiency, productivity, and automation of agricultural processes. As technology continues to advance, gears and gearboxes will continue to evolve, further enhancing the capabilities and performance of livestock equipment and greenhouse automation systems, driving the agriculture industry towards increased efficiency and sustainability.
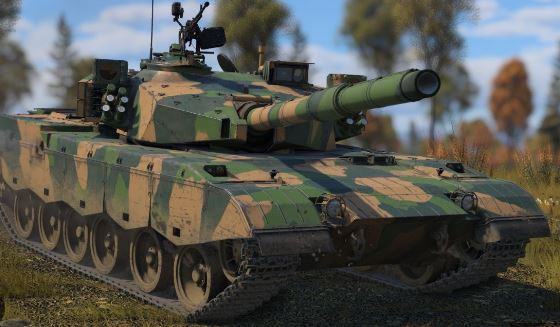
The Role of Gears and Gearboxes in Tanks
Tanks are powerful military vehicles designed for combat on the battlefield. Within these armored machines, gears and gearboxes are critical components that enable mobility, power transmission, and precise control. Gears facilitate the transfer of power from the engine to the tracks, while gearboxes provide speed adjustment and torque conversion. In this blog post, we will explore the significance of gears and gearboxes in tanks.
1. Track Propulsion: Gears and gearboxes play a crucial role in the propulsion system of tanks. Gears facilitate power transmission from the engine to the drive sprockets, which engage with the tracks, propelling the tank forward or backward. Gearboxes provide speed adjustment, allowing operators to control the rotational speed of the tracks. This enables tanks to traverse various terrains with efficiency and precision.
2. Steering and Maneuverability: Gears and gearboxes contribute to the steering and maneuvering capabilities of tanks. Tanks often employ differential steering, where the tracks on each side can move independently. Gears enable differential power distribution, allowing tanks to make precise turns and navigate challenging terrain. Gearboxes provide the necessary control over the rotational speed and torque applied to each track, ensuring smooth and responsive maneuverability.
3. Speed Control: Effective speed control is essential in tank operations. Gears and gearboxes offer speed control capabilities by providing different gear ratios. Tank operators can adjust the gear ratio to achieve the desired speed, whether it’s for rapid movement during offensive operations or slow and controlled movement for defensive or reconnaissance purposes. Gearboxes allow for precise speed adjustment, ensuring tanks can operate efficiently at different speeds.
4. Torque Conversion: Tanks require significant torque to overcome obstacles and operate in challenging terrain. Gears and gearboxes facilitate torque conversion by adjusting the rotational force transmitted to the tracks. They enable tanks to generate the necessary torque to climb steep slopes, traverse rough terrains, or push through obstacles. Efficient torque conversion enhances the mobility and operational capabilities of tanks in various combat scenarios.
5. Durability and Reliability: Tanks operate in harsh and demanding environments, subject to extreme temperatures, vibrations, and combat conditions. Gears and gearboxes used in tanks are designed to withstand these rigorous conditions. They are constructed with durable materials and precision engineering to ensure reliability and longevity. Regular maintenance and lubrication of gears and gearboxes are crucial to minimize wear and tear, ensuring optimal performance and maximizing the lifespan of tanks.
Gears and gearboxes are integral components in tanks, enabling track propulsion, steering, speed control, torque conversion, durability, and reliability. Their presence ensures the mobility, maneuverability, and operational effectiveness of tanks on the battlefield. As military technology continues to advance, gears and gearboxes will play a crucial role in enhancing the capabilities and performance of tanks, contributing to the armored forces’ effectiveness and success in modern warfare.
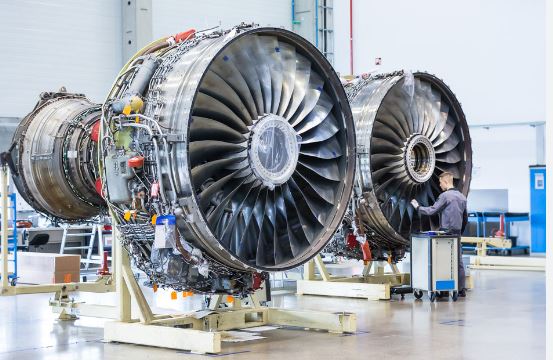
The Role of Gears and Gearboxes in the Aviation Industry
The aviation industry is known for its constant pursuit of innovation and advanced engineering solutions. Aircraft are equipped with numerous complex systems and components to enable safe and efficient travel through the air. One such crucial component is gears and gearboxes. Gears play a vital role in the aviation industry and have a significant impact on the performance, safety, and durability of aircraft. In this blog post, we will explore why gears and gearboxes are important in the aviation industry.
1. Power Transmission: Aircraft require effective transmission of power to propel and control their movement. Gears and gearboxes are integral in this power transmission process. They play a key role in transmitting power from the engines to various systems, such as the propellers or jet engines. Gears allow the engines to transfer rotational motion to generate thrust, enabling the aircraft to accelerate, climb, and maneuver. Gearboxes help in controlling the speed and torque of the engines, ensuring optimal performance and fuel efficiency.
2. Reduction of Rotational Speed: In aviation, engines typically operate at very high rotational speeds, while other aircraft systems require lower speeds for optimal functioning. Gears and gearboxes are used to reduce the rotational speed of the engines and transmit it to different components, such as generators, hydraulic pumps, or flight control systems. By reducing the rotational speed, gears and gearboxes enable these systems to operate efficiently and safely within their designed parameters.
3. Mechanical Advantage and Force Multiplication: Gears are renowned for their ability to provide mechanical advantage and force multiplication. In the aviation industry, this is particularly important for flight control systems. By utilizing gears and gearboxes, the pilot’s input can be translated into precise and amplified movement of control surfaces such as ailerons, elevators, and rudders. This allows for responsive and accurate control of the aircraft during various flight phases, including takeoff, landing, and maneuvering.
4. Load Distribution and Durability: Aircraft engines generate immense power and torque, which can place significant stress on various components. Gears and gearboxes aid in distributing the load and reducing stress on critical parts, improving overall durability and longevity. They help balance the forces acting on the engines and enable the aircraft to withstand high-stress conditions, such as during rapid acceleration or sudden changes in flight trajectory.
5. Backup and Redundancy: Reliability and redundancy are paramount in aviation to ensure the safety of passengers and crew. Gears and gearboxes play a crucial role in providing backup systems. In the event of a failure in the primary gear system, redundant gear sets or gearboxes can be engaged to maintain the functionality of essential systems. This redundancy ensures that even in the face of mechanical issues, the aircraft can continue to operate safely until maintenance or repairs can be performed.
Gears and gearboxes are indispensable components in the aviation industry. From power transmission and force multiplication to load distribution and redundancy, they play a vital role in ensuring safe and efficient aircraft operations. The continuous advancements in gear technology contribute to the overall improvement in aircraft performance, reliability, and passenger safety in the dynamic world of aviation.

The Role of Gears and Gearboxes in the Construction Industry
The construction industry is a dynamic sector that involves the creation of infrastructure and buildings. Within this industry, gears and gearboxes play a crucial role in various construction machinery and equipment, facilitating efficient and powerful operation. Gears enable power transmission and motion control, while gearboxes provide speed adjustment and torque conversion. In this blog post, we will explore the significance of gears and gearboxes in the construction industry.
1. Heavy Equipment Power Transmission: Construction sites require a wide range of heavy machinery, such as excavators, cranes, and bulldozers, to perform tasks like digging, lifting, and moving heavy materials. Gears and gearboxes are essential in transmitting power from the engines to the various components of these machines. They ensure that the rotational motion produced by the engine is effectively transferred to drive the movement of the equipment, providing the necessary power for construction operations.
2. Speed Control and Torque Conversion: Gears and gearboxes offer speed control and torque conversion capabilities in construction machinery. Different construction tasks require varying speeds and torque levels to meet specific requirements. Gears and gearboxes allow operators to adjust the gear ratio to achieve the desired speed and torque output, enabling precise control over the equipment’s performance. This versatility enhances the efficiency and effectiveness of construction operations, ensuring optimal productivity.
3. Cranes and Lifting Equipment: Cranes and lifting equipment are indispensable in the construction industry for lifting and moving heavy loads. Gears and gearboxes are critical components in these machines, providing the necessary power transmission and control for the lifting mechanisms. They ensure smooth and precise lifting operations, allowing for safe and efficient movement of materials and equipment at construction sites. Gearboxes enable operators to adjust the lifting speed and control the load with accuracy and precision.
4. Concrete Mixers and Pumps: Concrete mixers and pumps are commonly used in construction projects for preparing and delivering concrete to the desired locations. Gears and gearboxes are essential in these machines to facilitate the mixing and pumping processes. They ensure the proper rotation and movement of the mixing drum and pump components, enabling the consistent and efficient delivery of concrete to the construction site. Gearboxes offer the ability to adjust the speed and torque to match the specific requirements of the task.
5. Durability and Reliability: Construction sites often present challenging and demanding conditions, including heavy loads, vibrations, and rough terrains. Gears and gearboxes used in construction machinery are designed to withstand these rigorous environments. They are built with sturdy materials and precision engineering to ensure durability and reliability. Proper maintenance and lubrication of gears and gearboxes contribute to their longevity, minimizing downtime and maximizing the productivity of construction operations.
Gears and gearboxes play a vital role in the construction industry, enabling power transmission, speed control, and torque conversion in various construction machinery and equipment. From heavy equipment power transmission to the precise control of cranes and concrete mixers, gears and gearboxes are essential components that contribute to the efficiency and effectiveness of construction operations. As the construction industry continues to evolve, advancements in gear and gearbox technology will further enhance productivity, safety, and sustainability, driving the future of construction towards more innovative and efficient practices.
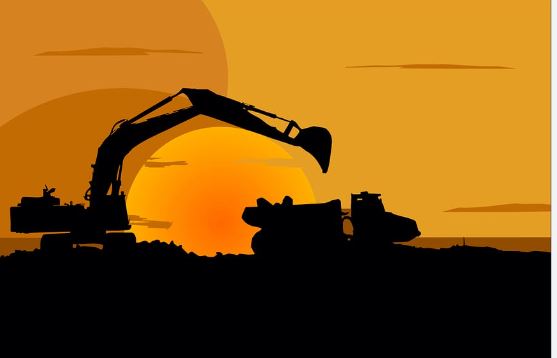
The Role of Gears and Gearboxes in the Heavy Equipment Industry
The heavy equipment industry plays a vital role in various sectors, including construction, mining, agriculture, and transportation. Within this industry, gears and gearboxes are crucial components used in heavy equipment to facilitate powerful and efficient operations. Gears enable power transmission and motion control, while gearboxes provide speed adjustment and torque conversion. In this blog post, we will explore the significance of gears and gearboxes in the heavy equipment industry.
1. Power Transmission: Gears and gearboxes are integral to power transmission in heavy equipment. From excavators and bulldozers to cranes and dump trucks, gears facilitate the transfer of power from the engine to various components, such as wheels, tracks, or lifting mechanisms. They ensure that the rotational motion produced by the engine is efficiently transferred to drive the movement and operation of the equipment, providing the necessary power for heavy-duty tasks.
2. Speed Control: Speed control is crucial in heavy equipment operations to match the requirements of different tasks and conditions. Gears and gearboxes offer the ability to adjust speed by providing different gear ratios. Operators can change gears to achieve the desired speed for specific operations, such as digging, lifting, or hauling. Gearboxes allow for speed adjustment and optimization, ensuring the equipment operates efficiently and safely in various working environments.
3. Torque Conversion: Heavy equipment often requires torque conversion to handle different loads and perform tasks effectively. Gears and gearboxes facilitate torque conversion by adjusting the rotational force transmitted to the equipment’s components. They enable the equipment to generate the necessary torque for tasks such as digging, lifting, or pushing heavy loads. The ability to convert torque efficiently enhances the performance and productivity of heavy equipment, allowing operators to handle demanding tasks with ease.
4. Load Handling and Material Movement: Heavy equipment is designed to handle substantial loads and move materials efficiently. Gears and gearboxes play a crucial role in this aspect by providing power transmission and control for lifting, hauling, or material handling operations. Whether it’s a crane lifting heavy objects or a loader moving materials, gears and gearboxes enable smooth and precise movement, ensuring efficient and safe handling of loads.
5. Durability and Reliability: Heavy equipment operates in demanding environments, exposed to extreme temperatures, rough terrains, and heavy loads. Gears and gearboxes used in heavy equipment are built to withstand these rigorous conditions. They are designed with durable materials and precision engineering to ensure durability and reliability. Proper maintenance and lubrication of gears and gearboxes are essential for their longevity, minimizing downtime and maximizing the productivity of heavy equipment operations.
Gears and gearboxes are essential components in the heavy equipment industry, enabling power transmission, speed control, and torque conversion in various equipment types. From excavators and loaders to cranes and dump trucks, gears and gearboxes contribute to the efficiency, productivity, and reliability of heavy equipment operations. As the heavy equipment industry continues to evolve, advancements in gear and gearbox technology will further enhance performance, safety, and sustainability, driving the future of heavy equipment towards more innovative and efficient practices.
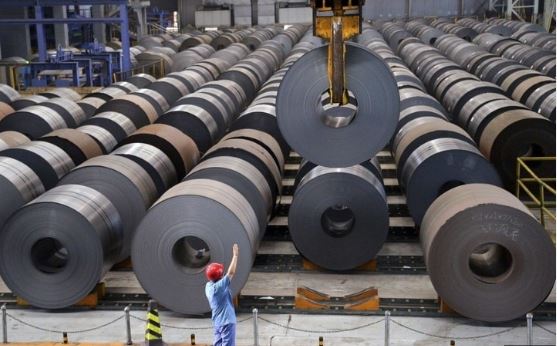
The Role of Gears and Gearboxes in the Iron and Steel Industry
The iron and steel industry plays a critical role in the production of essential materials for various sectors, including construction, automotive, and manufacturing. Within this industry, gears and gearboxes are vital components used in iron and steel manufacturing processes to ensure efficient and reliable operations. Gears facilitate power transmission and motion control, while gearboxes provide speed adjustment and torque conversion. In this blog post, we will explore the importance of gears and gearboxes in the iron and steel industry.
1. Rolling Mills: Rolling mills are essential in the iron and steel industry for the shaping and forming of metal products. Gears and gearboxes are crucial components in rolling mills, enabling the transmission of power to roll stands. They ensure the proper rotation and movement of rolls, which shape and reduce the thickness of metal sheets or billets. Gearboxes offer speed control and torque conversion, allowing operators to adjust rolling speeds and apply the required pressure for various metal-forming processes.
2. Continuous Casting: Continuous casting is a widely used method in the iron and steel industry to produce high-quality steel products. Gears and gearboxes are integral in continuous casting machines, which convert molten steel into solid billets or slabs. Gears facilitate the smooth movement of the casting molds, while gearboxes provide the necessary power transmission and speed control. Precise control over the casting process ensures consistent product quality and minimizes waste.
3. Cranes and Material Handling: Iron and steel manufacturing involves the movement and handling of heavy loads, such as molten metal, raw materials, and finished products. Gears and gearboxes play a crucial role in cranes and material handling equipment, providing power transmission and torque conversion for lifting, moving, and positioning heavy loads. They enable precise control and safe operation of cranes, ensuring efficient material handling throughout the iron and steel production process.
4. Steelmaking Processes: Steelmaking processes, such as blast furnaces and electric arc furnaces, require efficient power transmission and control for their operation. Gears and gearboxes are utilized in these processes to transmit power from motors or engines to various components, such as blowers, pumps, or electrode positioners. Gearboxes enable speed adjustment and torque conversion to optimize the performance of steelmaking equipment, ensuring efficient and reliable production.
5. Durability and Reliability: The iron and steel industry operates under demanding conditions, including high temperatures, heavy loads, and extreme pressures. Gears and gearboxes used in this industry are designed to withstand these rigorous environments. They are built with robust materials and precision engineering to ensure durability and reliability. Proper lubrication and maintenance of gears and gearboxes are essential for their longevity, minimizing downtime and maximizing the productivity of iron and steel manufacturing processes.
Gears and gearboxes are vital components in the iron and steel industry, enabling power transmission, speed control, and torque conversion in various manufacturing processes. From rolling mills to continuous casting machines and material handling equipment, gears and gearboxes contribute to the efficiency, productivity, and quality of iron and steel production. As the industry continues to evolve, advancements in gear and gearbox technology will further enhance productivity, sustainability, and operational reliability, driving the future of the iron and steel industry towards more innovative and efficient practices.
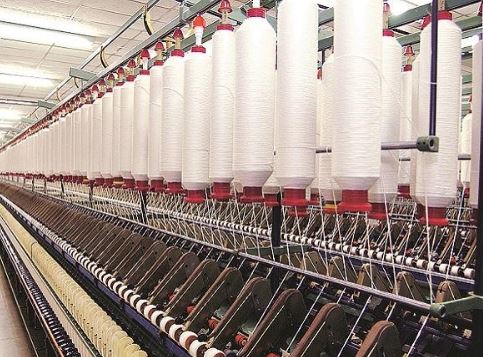
The Role of Gears and Gearboxes in the Textile Industry
The textile industry is a dynamic sector that involves the manufacturing of fibers, fabrics, and various textile products. Within this industry, gears and gearboxes are essential components used in textile machinery to facilitate efficient production processes. Gears enable the transmission of power and motion, while gearboxes provide speed control and torque conversion. In this blog post, we will explore the significance of gears and gearboxes in the textile industry.
1. Power Transmission: Gears and gearboxes play a crucial role in power transmission within textile machinery. From spinning machines to weaving looms, gears are responsible for transmitting power from the motor to various components, such as spindles, rollers, and shafts. They ensure that the necessary rotational motion is efficiently transferred to drive the production process. Gears help maintain consistent speed and torque, resulting in uniform and high-quality textile output.
2. Speed Control: Speed control is vital in textile manufacturing to achieve desired results and maintain product quality. Gears and gearboxes enable speed control by providing different gear ratios. By changing gears, textile machinery can operate at various speeds, accommodating different fabric types, yarn thicknesses, and production requirements. Gearboxes allow operators to adjust the rotational speed of critical components, ensuring precise control over the manufacturing process.
3. Torque Conversion: Textile machinery often requires torque conversion to handle different types of fabrics and manufacturing stages. Gears and gearboxes facilitate torque conversion by adjusting the rotational force transmitted to the components. They allow textile machines to generate the appropriate level of torque for specific tasks, such as yarn winding, fabric stretching, or thread tensioning. The ability to convert torque efficiently enhances the overall performance and productivity of textile machinery.
4. Durability and Reliability: Textile manufacturing involves repetitive and demanding operations, subjecting machinery to significant stress and wear. Gears and gearboxes designed for the textile industry are built to withstand these challenging conditions. They are manufactured with high-quality materials and precision engineering to ensure durability and reliability. Proper lubrication and maintenance of gears and gearboxes contribute to extending their lifespan and minimizing downtime in the production process.
5. Customization and Specialized Applications: The textile industry encompasses a wide range of processes and applications, each with its unique requirements. Gears and gearboxes can be customized to meet specific needs, such as different gear profiles, sizes, or materials. This flexibility allows textile manufacturers to optimize their machinery for specialized applications, such as knitting, dyeing, or fabric finishing. Customized gears and gearboxes ensure precise control, efficiency, and consistency throughout the textile production cycle.
Gears and gearboxes are indispensable components in the textile industry, enabling power transmission, speed control, torque conversion, durability, and reliability in textile machinery. Their role in facilitating efficient production processes and maintaining product quality cannot be overstated. As the textile industry continues to evolve, advancements in gear and gearbox technology will further enhance productivity, customization, and sustainability, contributing to the growth and innovation of this dynamic sector.
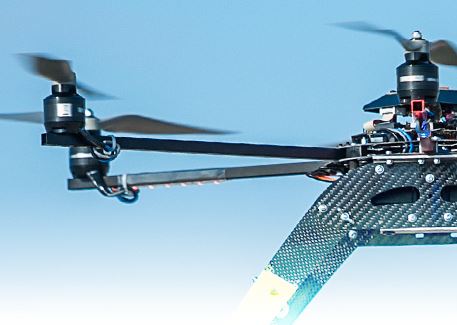
The Role of Gears in Unmanned Aerial Vehicles (UAVs)
Unmanned Aerial Vehicles (UAVs), commonly known as drones, have revolutionized various industries, including aerial photography, delivery services, surveillance, and agriculture. Within these UAVs, gears play a critical role in enabling efficient and precise flight control. Gears facilitate power transmission and motion control, ensuring smooth and reliable operation. In this blog post, we will explore the significance of gears in unmanned aerial vehicles.
1. Flight Control: Gears are essential components in the flight control systems of UAVs. They enable the transmission of power from the motors to the propellers, which generate the necessary thrust for flight. Gears ensure that the rotational motion produced by the motors is efficiently transferred to the propellers, resulting in precise control over the UAV’s movement, including ascent, descent, and directional changes.
2. Speed Control: Controlling speed is crucial in UAVs to achieve stable flight and maneuverability. Gears offer speed control capabilities by providing different gear ratios. By changing gears, UAV operators can adjust the rotational speed of the propellers, allowing for varying flight speeds based on specific requirements. Speed control through gears enables UAVs to optimize their performance for different tasks, such as aerial photography, search and rescue, or surveillance.
3. Torque Conversion: UAVs often require torque conversion to adapt to changing flight conditions or payload requirements. Gears facilitate torque conversion by adjusting the rotational force transmitted to the propellers. This allows UAVs to generate the necessary thrust to overcome external forces, such as wind resistance, or to carry heavier payloads. Proper torque conversion ensures efficient flight performance and stability in diverse operating conditions.
4. Durability and Efficiency: Gears used in UAVs are designed to be lightweight yet durable to maximize flight efficiency and endurance. They are constructed using high-quality materials, such as aluminum alloys or composites, to ensure strength and reliability while minimizing weight. The use of durable gears contributes to the overall longevity and operational efficiency of UAVs, enabling longer flight times and reducing maintenance requirements.
5. Noise Reduction: In addition to their functional role, gears also impact the acoustic performance of UAVs. Noise reduction is a critical consideration, especially in applications such as aerial photography or surveillance, where minimizing noise interference is essential. Carefully designed and properly lubricated gears can help reduce noise levels generated by the propulsion system, resulting in quieter operation and improved overall performance.
Gears are integral components in unmanned aerial vehicles (UAVs), enabling flight control, speed adjustment, torque conversion, durability, and noise reduction. Their presence ensures precise and efficient operation, allowing UAVs to perform various tasks with stability and reliability. As UAV technology continues to advance, gears will continue to play a vital role in enhancing flight performance, autonomy, and versatility, driving the future of unmanned aerial vehicles toward new possibilities in different industries.