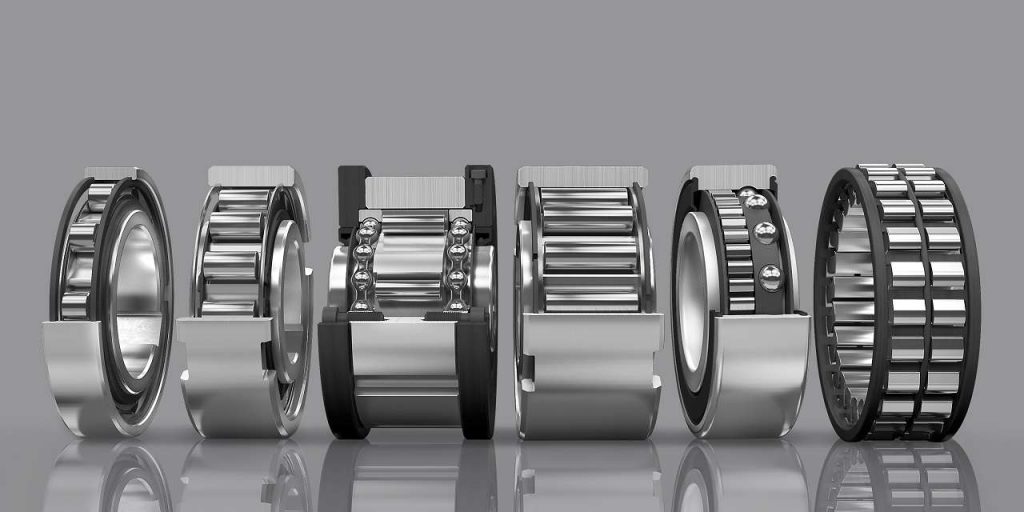
Backstops
Backstops are an essential component in many mechanical systems, particularly those involving rotating machinery. These devices are designed to prevent the reverse rotationof a shaft, and they are commonly used in applications like conveyor systems, cranes, and various types of equipment in the mining and energy industries. In this blog post, we will take a closer look at backstops, how they work, their advantages, and their applications.
How Backstops Work:
Backstops work by using a combination of mechanical and spring-loaded mechanisms to lock the rotational movement of a shaft in one direction. When the shaft rotates in theforward direction, the backstop allows it to pass through freely. However, when theshaft begins to rotate in the opposite direction, the backstop engages and locks it in place, preventing it from rotating any further.
Backstops typically have two main components: the inner and outer races. The innerrace is typically connected to the shaft, while the outer race is stationary. The spring-loaded mechanism is located between these two races, allowing for the backstop toengage or disengage depending on the direction of rotation.
Advantages of Backstops:
Backstops offer several advantages over other types of mechanical systems. Theseinclude:
Applications of Backstops:
Backstops are used in a wide variety of applications, including:
Conclusion:
Backstops are an essential component in many mechanical systems, providing addedsafety, improved efficiency, and durability. They work by using a combination of mechanical and spring-loaded mechanisms to prevent reverse rotation of a shaft. Backstops are used in a variety of applications, including conveyor systems, cranes, theenergy industry, and mining. With their ability to prevent reverse rotation and enhanceoverall system safety and efficiency, backstops are a critical component in many rotatingmachinery applications.
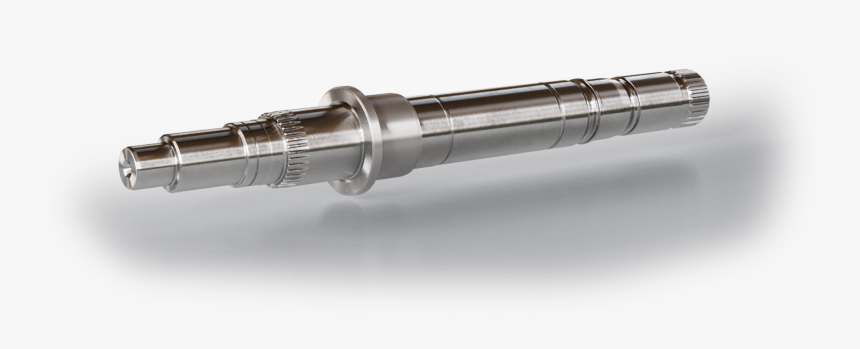
The Manufacturing Process of Shaft
Shaft manufacturing is the process of creating a long, cylindrical component used fortransmitting power from one part of a machine to another. Shafts are commonly foundin engines, pumps, and other mechanical devices, and can be made from a variety of materials including steel, aluminum, and titanium.
The manufacturing process for shafts typically involves the following steps:
1.Material selection: The material for the shaft is chosen based on the applicationrequirements such as strength, weight, and durability.
2.Cutting and shaping: The raw material is cut into the appropriate length anddiameter using cutting tools such as saws, lathes, and milling machines.
3.Machining: The shaft is then machined to the desired dimensions using a variety of cutting tools and techniques, such as turning, drilling, grinding, and honing. This process creates a smooth, uniform surface on the shaft that is necessary for properoperation.
4.Heat treatment: The shaft may undergo heat treatment to improve its strengthand durability. This involves heating the shaft to a high temperature and then cooling it rapidly to create a hardened surface layer.
5.Surface finishing: The shaft is finished with a surface treatment such as polishing, plating, or coating to improve its appearance and protect it from corrosion.
6.Inspection: The shaft is inspected for defects and dimensional accuracy usingspecialized equipment such as gauges, micrometers, and surface finish testers.
Overall, the manufacturing process for shafts is complex and requires a high level of precision and expertise to ensure that the final product meets the necessary quality standards.