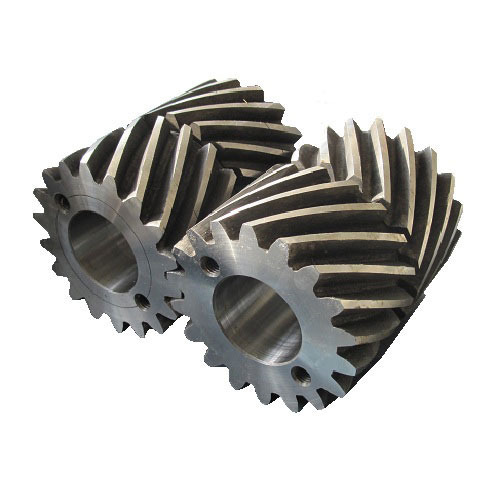
Herringbone Gear
Herringbone gears, also known as double helical gears, are a type of gear commonlyused in heavy-duty industrial applications. They are characterized by their unique V-shaped teeth that allow for greater load carrying capacity and smoother operation thantraditional spur gears.
How Do Herringbone Gears Work?
Herringbone gears consist of two helical gears that are mounted adjacent to each otherwith opposing helix angles. This design creates a V-shaped tooth profile that eliminatesthe axial thrust generated by traditional helical gears. As a result, herringbone gears can handle greater loads and operate more smoothly and quietly than their helicalcounterparts.
Advantages of Herringbone Gears
Applications of Herringbone Gears
Herringbone gears are commonly used in heavy-duty industrial applications, such as:
Conclusion
Herringbone gears are a critical component of many heavy-duty industrial applicationsthat require high torque and load carrying capacity. Their unique V-shaped toothprofile and opposing helix angles provide several advantages over traditional spur orhelical gears, including greater load capacity, smoother operation, increased efficiency, and better heat dissipation. With their broad range of applications and benefits, herringbone gears are an essential component of many mechanical systems that requireprecise and reliable power transmission.
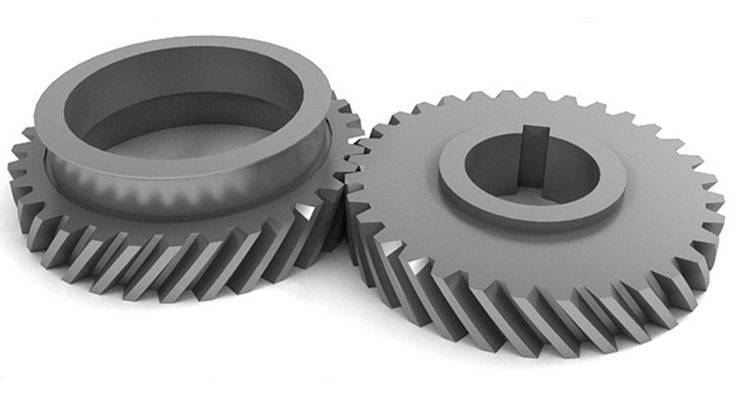
Helical Gear
Helical gears are a type of gear that is widely used in mechanical power transmissionsystems. They are characterized by their unique tooth geometry, which is helical ortwisted in shape. This design provides several advantages over other types of gears, including increased load capacity, smoother operation, and reduced noise and vibration.
How Do Helical Gears Work?
Helical gears work by transferring rotational power from one shaft to another through a series of interlocking teeth. The teeth on a helical gear are cut at an angle to the gear’saxis, resulting in a twisted or helical shape. When two helical gears are meshed together, the helical teeth form a diagonal contact pattern, which spreads the load across a largersurface area than other types of gears.
Advantages of Helical Gears
Applications of Helical Gears
Helical gears are used in a wide range of applications, including:
Conclusion
Helical gears are a versatile and reliable type of gear that is widely used in mechanicalpower transmission systems. Their unique tooth geometry provides several advantagesover other types of gears, including increased load capacity, smoother operation, andreduced noise and vibration. With their broad range of applications and benefits, helicalgears are a critical component of many mechanical systems.
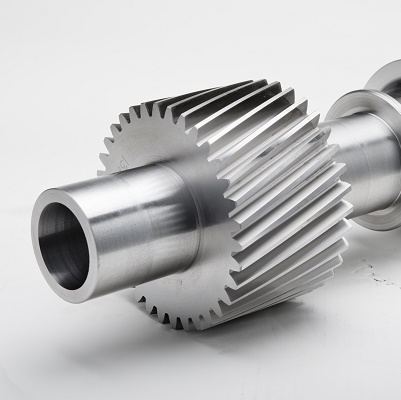
Ground Gear
Ground gears are a type of gear that is produced by grinding instead of cutting. Thisgrinding process creates a more precise and consistent gear than traditional cuttingmethods. In this blog post, we will explore the advantages and applications of groundgears.
Advantages of Ground Gears
Applications of Ground Gears
Conclusion
Ground gears are a high-precision and high-strength gear system that is ideal for a widerange of applications. With their precise tooth profile, smooth operation, high strength, and reduced friction, ground gears are a reliable and efficient choice for aerospace, automotive, industrial, and robotics applications. Ground gears provide the necessaryprecision and durability for critical applications that require precise motion control andhigh load capacity.
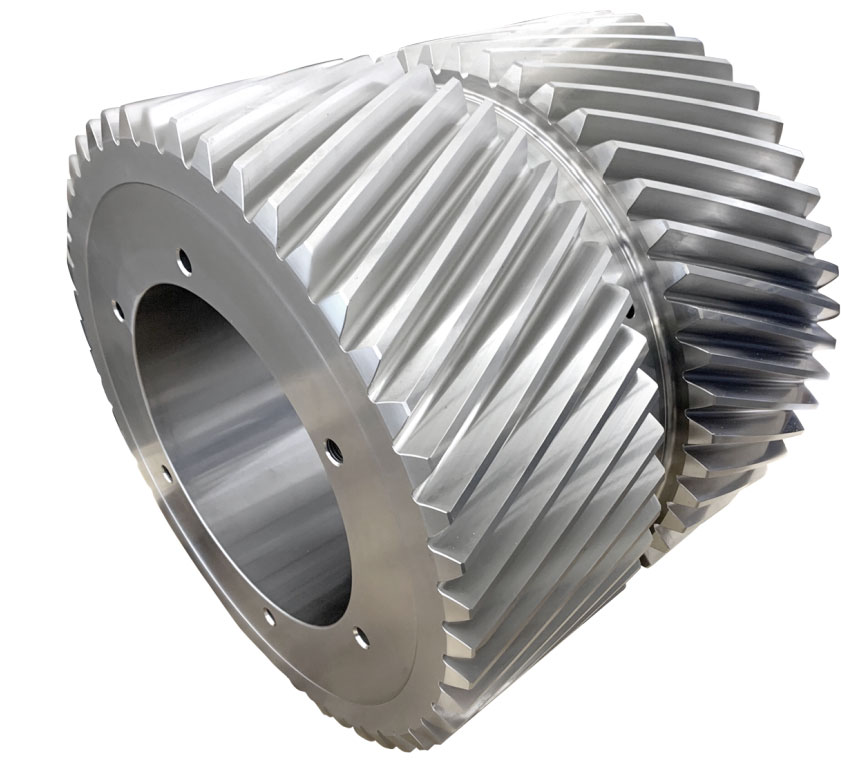
Double Helical Gears
Double helical gears, also known as herring bone gears, are a type of gear with two setsof helical teeth that are cut in opposite directions. This design eliminates the axial thrustthat is generated by helical gears with a single set of teeth, making them ideal for high-speed, high-torque applications where precise and reliable power transmission is critical.
How Do Double Helical Gears Work?
Double helical gears work by transmitting rotational power from one shaft to anotherthrough a series of interlocking teeth. Unlike helical gears with a single set of teeth, double helical gears have two sets of helical teeth that are cut in opposite directions. Thiscreates a V-shaped groove between the teeth that eliminates the axial thrust that is generated by single helical gears.
Advantages of Double Helical Gears
Applications of Double Helical Gears
Double helical gears are used in a variety of high-speed, high-torque applications, including:
Conclusion
Double helical gears are a critical component of many high-speed, high-torquemechanical power transmission systems. Their unique design provides severaladvantages over other types of gears, including reduced noise and vibration, increasedload capacity, improved precision, and greater efficiency. With their broad range of applications and benefits, double helical gears are an essential component of manymechanical systems that require precise and reliable power transmission.
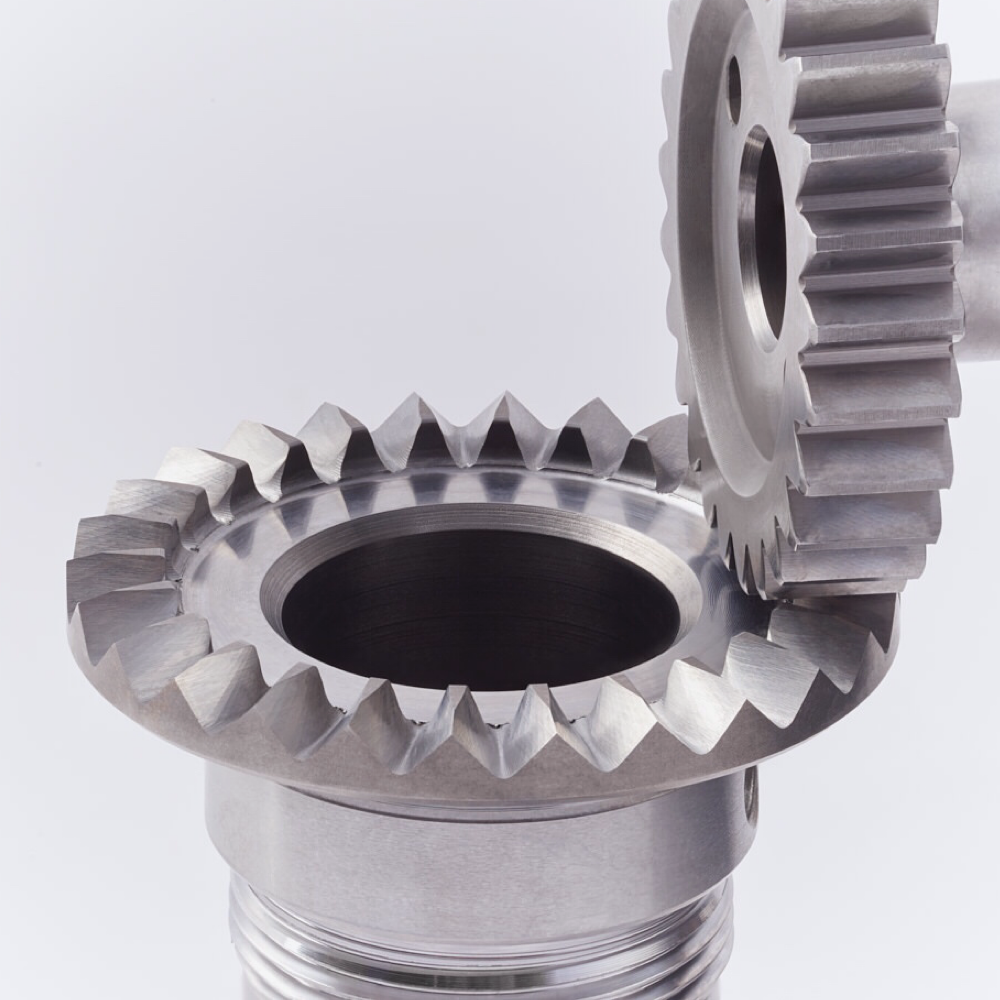
Crowned Gear
Crowned gears are specialized gears that are used in applications where misalignmentbetween the driving and driven shafts is likely to occur. They are commonly used in equipment such as conveyors, printing presses, and packaging machinery, where precisealignment is crucial for optimal performance.
What are Crowned Gears?
Crowned gears are gears that have a specially designed tooth profile that is slightlycurved or tapered towards the center of the gear. This design allows the gear toaccommodate small misalignments between the driving and driven shafts while stillmaintaining constant contact between the teeth of the gears. The slight curve or taper of the tooth profile ensures that the gears only touch at their highest point, which reduceswear and tear on the gear teeth and extends their lifespan.
Applications of Crowned Gears
Crowned gears are commonly used in applications where precise alignment is difficult toachieve or maintain. They are particularly useful in equipment that is subject to changesin temperature, vibration, or other environmental factors that can cause misalignmentbetween the driving and driven shafts.
Some of the common applications of crowned gears include:
Benefits of Crowned Gears
The benefits of using crowned gears in equipment are numerous. Some of the keybenefits include:
In conclusion, crowned gears are a specialized type of gear that is designed toaccommodate misalignment between the driving and driven shafts. They are commonlyused in a wide range of industrial applications and can help to improve equipmentperformance, increase lifespan, and reduce downtime. By understanding the benefits of crowned gears, equipment operators can select the right type of gear for their specificapplication and ensure optimal performance and reliability.
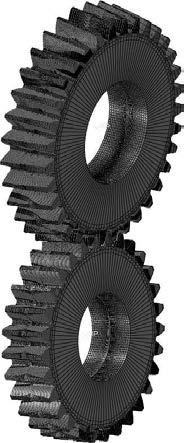
Bevel Oid Gear
Bevel oid gears are a type of bevel gear that have curved teeth rather than straight teeth. This unique design allows for smoother, quieter operation and improved load carrying capacity compared to traditional straight-tooth bevel gears. Beveloid gears are widelyused in a variety of applications, including automotive, aerospace, and industrialmachinery.
How Do Bevel oid Gears Work?
Bevel oid gears are designed to transmit rotational power between two intersecting shaftsthat are not parallel to one another. The teeth of a beveloid gear are cut at an angle tothe axis of the gear, which allows the gear to mesh with another beveloid gear or a straight-tooth bevel gear. Beveloid gears can be either external or internal, dependingon whether the teeth are located on the outer or inner surface of the gear.
Advantages of Bevel oid Gears
Applications of Bevel oid Gears
Beveloid gears are used in a wide range of applications, including:
Conclusion
Bevel oid gears are a critical component of many mechanical power transmissionsystems. Their unique design provides several advantages over traditional straight-toothbevel gears, including improved load carrying capacity, reduced noise and vibration, greater design flexibility, and improved efficiency. With their broad range of applications and benefits, beveloid gears are an essential component of manymechanical systems that require precise and reliable power transmission.
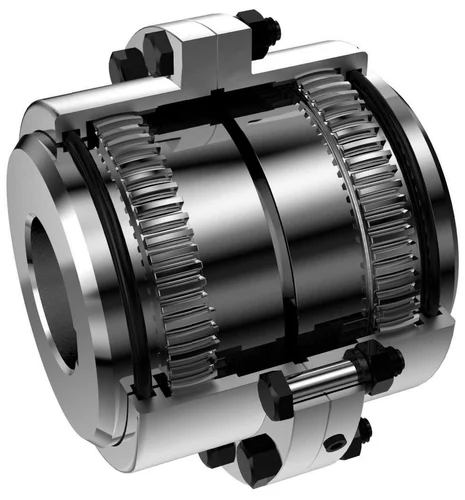
Gear Couplings
Gear couplings are a type of flexible coupling used to connect two rotating shafts, allowing for a smooth transfer of power and torque between them. They consist of two gear teeth, one on each shaft, which mesh together to transmit power from one shaft to the other. Gear couplings are widely used in various applications, including steel mills, paper mills, and other heavy industries where high torque and precision are required.
In this blog post, we’ll take a closer look at gear couplings, how they work, their advantages, and their applications.
How Gear Couplings Work: Gear couplings consist of two hubs with external teeth thatmesh together to transmit power. The hubs are made of high-strength steel and aredesigned to withstand high torque and loads. The hubs are connected by a flexible sleevethat compensates for misalignment and absorbs shock loads.
The flexible sleeve can be made of different materials, including metallic, non-metallic, and composite materials. The most commonly used material for the flexible sleeve is metallic, which is made of stainless steel, bronze, or other alloys. Non-metallic sleevescan also be used in some applications, such as food processing or pharmaceuticals, where contamination is a concern.
Gear couplings work by transmitting torque through the meshing of the external teethon the hubs. The teeth are cut to precision to ensure proper alignment and reduce wearand tear. Gear couplings can accommodate different types of misalignments, includingangular, radial, and axial misalignments. This makes them ideal for applications wherehigh torque and precision are required.
Advantages of Gear Couplings:
Gear couplings offer several advantages over othertypes of couplings. These include:
Applications of Gear Couplings:
Gear couplings are used in various applications, including:
Conclusion: Gear couplings are a type of flexible coupling widely used in heavyindustrial applications where high torque and precision are required. They offer severaladvantages over other types of couplings, including high torque capacity, high precision, flexibility, durability, and easy maintenance. Gear couplings are used in variousapplications, including steel mills, paper mills, chemical plants, and marine applications.
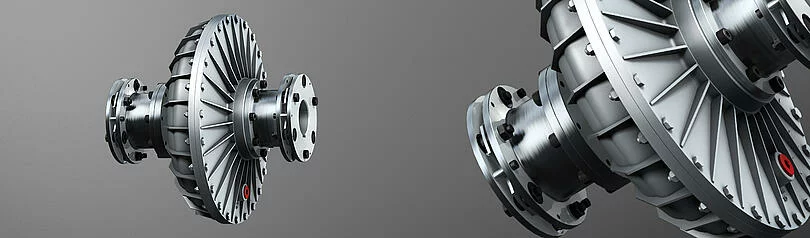
Fluid Couplings
Fluid couplings are a type of hydraulic coupling used to transmit power and torque between two rotating shafts. They consist of an impeller and a runner, both of which areen closed in a housing filled with hydraulic fluid. Fluid couplings are widely used in various applications, including mining, cement, and power generation, where they offer high efficiency and smooth power transmission.
In this blog post, we’ll take a closer look at fluid couplings, how they work, their advantages, and their applications.
How Fluid Couplings Work: Fluid couplings work on the principle of hydraulic torquemultiplication. The impeller, which is connected to the driving shaft, rotates and createsa flow of hydraulic fluid inside the housing. The hydraulic fluid then transfers torque tothe runner, which is connected to the driven shaft.
Fluid couplings use hydraulic fluid to transfer torque and allow for a smooth start andstop of the driven equipment. The hydraulic fluid in the coupling also acts as a damping mechanism, reducing shock loads and vibrations during operation.
Fluid couplings have three main components: the impeller, the runner, and the housing. The impeller is the driving component and is connected to the driving shaft. The runneris the driven component and is connected to the driven shaft. The housing encloses theimpeller and runner and contains the hydraulic fluid.
Advantages of Fluid Couplings:
Fluid couplings offer several advantages over othertypes of couplings. These include:
Applications of Fluid Couplings:
Fluid couplings are used in various applications, including:
Conclusion: Fluid couplings are a type of hydraulic coupling widely used in variousapplications, including mining, cement, and power generation. They offer severaladvantages over other types of couplings, including smooth power transmission, highefficiency, overload protection, low maintenance, and flexibility. Fluid couplings areused in different applications, including mining equipment, cement plants, powergeneration, and marine applications, where they provide a reliable and efficient meansof transmitting power and torque.
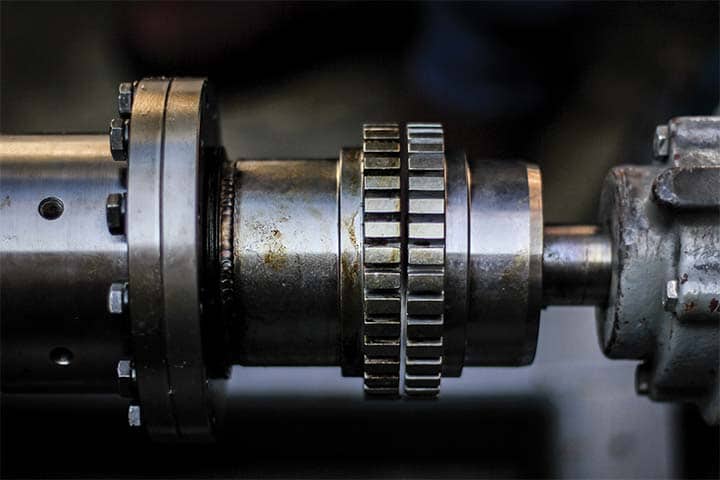
Uses of Couplings and Backstops
Couplings and backstops are two important components used in mechanical powertransmission systems.
A coupling is a device used to connect two shafts together in order to transmit powerfrom one shaft to the other. Couplings are used to compensate for shaft misalignment, absorb shock and vibration, and protect machinery from overload. There are varioustypes of couplings including rigid couplings, flexible couplings, and fluid couplings. Rigid couplings are used when shaft alignment is accurate, while flexible couplings areused when there is a slight misalignment between the shafts. Fluid couplings are used tosmoothly transmit power between two shafts.
A backstop is a device used to prevent the reverse rotation of a machine or equipment. Itis typically used in conveyors, hoists, and other machinery that needs to maintain itsposition when the power is turned off. Backstops are installed between the gearbox andthe motor to prevent the gearbox from rotating backwards. There are various types of backstops, including sprag clutches, roller clutches, and ratchet and pawl mechanisms.
In summary, couplings are used to connect two shafts together to transmit power andcompensate for shaft misalignment, while backstops are used to prevent the reverserotation of a machine or equipment. Both couplings and backstops play important rolesin mechanical power transmission systems.

Type of Couplings and Backstops and their features
There are various types of couplings and backstops used in mechanical power transmission systems, each with their own features and benefits. Here are some common types:
1.Rigid Couplings: Rigid couplings are used when shaft alignment is precise andthere is no need for compensation. They are typically made of metal and provide a solid, inflexible connection between two shafts.
2.Flexible Couplings: Flexible couplings are used when there is slightmisalignment between the shafts. They are designed to compensate for misalignment, absorb shock and vibration, and protect machinery from overload. Common types of flexible couplings include jaw couplings, gear couplings, and disc couplings.
3.Fluid Couplings: Fluid couplings are used to smoothly transmit power betweentwo shafts. They use hydraulic fluid to transmit torque from one shaft to the other, andcan also provide some degree of misalignment compensation.
4.Sprag Clutches: Sprag clutches are a type of backstop used to prevent thereverse rotation of a machine or equipment. They consist of a cylindrical outer race andan inner race with sprags (small angled teeth) that engage in one direction but allow freerotation in the opposite direction.
5.Roller Clutches: Roller clutches are another type of backstop that use rollersinstead of sprags to prevent reverse rotation. They are typically used in high-speedapplications and can handle high torque loads.
6.Ratchet and Pawl Mechanisms: Ratchet and pawl mechanisms are used toprevent reverse rotation in low-speed applications. They consist of a ratchet (a toothedwheel) and a pawl (a spring-loaded lever) that engage in one direction but allow freerotation in the opposite direction.
Overall, the choice of coupling or backstop will depend on the specific requirements of the application, such as the amount of misalignment that needs to be compensated for, the amount of torque that needs to be transmitted, and the speed and direction of rotation.