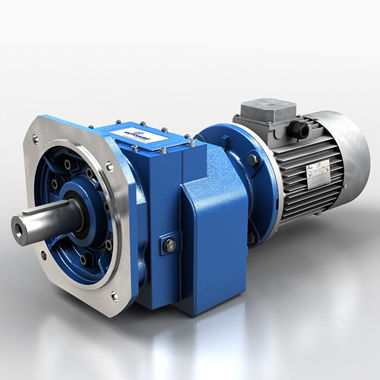
Helical Gear Reducer
Helical gear reducers are a type of power transmission equipment that are commonlyused in various industrial applications, including manufacturing, material handling, andprocessing. These gear reducers are designed to reduce the speed and increase thetorque of a motor, allowing it to drive heavy loads with ease.
In this blog post, we will take a closer look at helical gear reducers, their functions, types, and benefits.
Functions of Helical Gear Reducers
The primary function of a helical gear reducer is to reduce the speed of a motor whileincreasing its torque. This is achieved by using helical gears that mesh with each other at an angle, allowing them to transmit power smoothly and efficiently. The output shaft of the reducer is typically slower but has a higher torque than the input shaft, allowing it todrive heavy loads with ease.
Types of Helical Gear Reducers
There are several different types of helical gear reducers available on the market, eachdesigned for specific applications and operating conditions. Some of the most commontypes of helical gear reducers include:
Benefits of Helical Gear Reducers
Helical gear reducers offer several benefits over other types of power transmissionequipment. Some of the most significant benefits of helical gear reducers include:
In conclusion, helical gear reducers are an essential component in various industrialapplications. They are designed to reduce the speed of a motor while increasing itstorque, allowing it to drive heavy loads with ease. By understanding the functions, types, and benefits of helical gear reducers, users can select the right type of reducer for theirspecific application, ensuring maximum performance and efficiency.
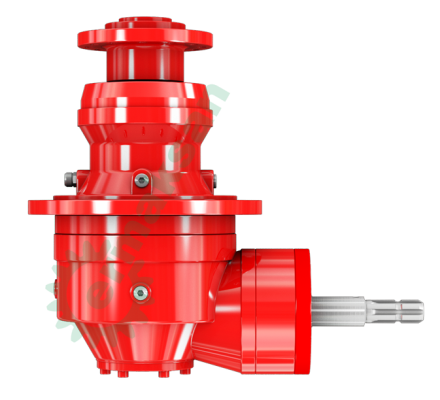
Feed Mixer Reducer
Feed mixer reducers, also known as feed mixer gearboxes, are a critical component in the animal feed industry. They are designed to mix different types of feed ingredients, including grains, vitamins, and minerals, to create a nutritious and well-balancedanimal feed. In this blog post, we will take a closer look at feed mixer reducers, theirfunction, features, and benefits.
Function of Feed Mixer Reducers:
Feed mixer reducers are designed to mix different types of animal feed ingredients, ensuring a uniform and consistent mixture. They work by receiving power from an electric motor, which is transmitted to the gearbox. The gearbox then reduces the speedof the motor and increases the torque to mix the feed ingredients thoroughly.
Features of Feed Mixer Reducers:
Feed mixer reducers come with a range of features, including:
Benefits of Feed Mixer Reducers:
Feed mixer reducers offer several benefits to the animal feed industry, including:
Applications of Feed Mixer Reducers:
Feed mixer reducers are used in a variety of animal feed applications, including:
Conclusion:
Feed mixer reducers are an essential component in the animal feed industry, ensuring a uniform and consistent mixture of different feed ingredients. They offer several benefits, including improved feed quality, increased efficiency, reduced labor costs, and greaterflexibility. With their high-quality materials, compact design, and customization options, feed mixer reducers are an ideal solution for the animal feed industry. They are used in poultry feed, livestock feed, and fish feed applications, ensuring that animals receive a nutritious and well-balanced diet.
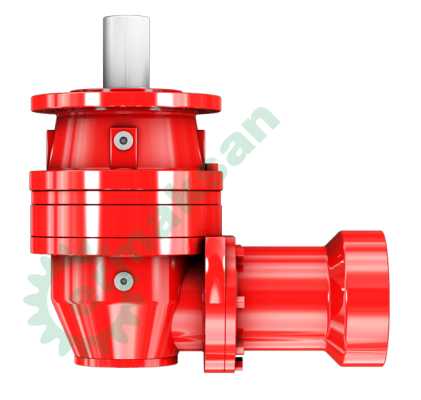
Elbow Reducers
Elbow reducers, also known as elbow reducers or elbow transition fittings, are an essential component in many piping systems. They are designed to connect pipes of different sizes and directions, allowing for smooth and efficient fluid flow. In this blog post, we will take a closer look at elbow reducers, how they work, their advantages, andtheir applications.
How Elbow Reducers Work:
Elbow reducers work by connecting pipes of different sizes and directions, allowing forfluid to flow efficiently through the system. They consist of two sections: an elbowsection that changes the direction of the pipe and a reducer section that reduces thepipe’s diameter.
Elbow reducers are available in different angles, including 45 degrees and 90 degrees, allowing for greater flexibility in piping system design. The angle of the elbow sectiondetermines the direction of the pipe, while the reducer section reduces the pipe’sdiameter to accommodate the smaller pipe size.
Advantages of Elbow Reducers:
Elbow reducers offer several advantages over other types of fittings, including:
Applications of Elbow Reducers:
Elbow reducers are used in a wide variety of applications, including:
Conclusion:
Elbow reducers are an essential component in many piping systems, allowing for theefficient flow of fluids through pipes of different sizes and directions. They are easy toinstall, cost-effective, and durable, making them an ideal solution for a wide variety of applications. Elbow reducers are commonly used in HVAC systems, plumbing systems, chemical processing, and food and beverage processing, among other applications. Withtheir ability to connect pipes of different sizes and directions, elbow reducers play a critical role in ensuring the smooth and efficient operation of many piping systems.
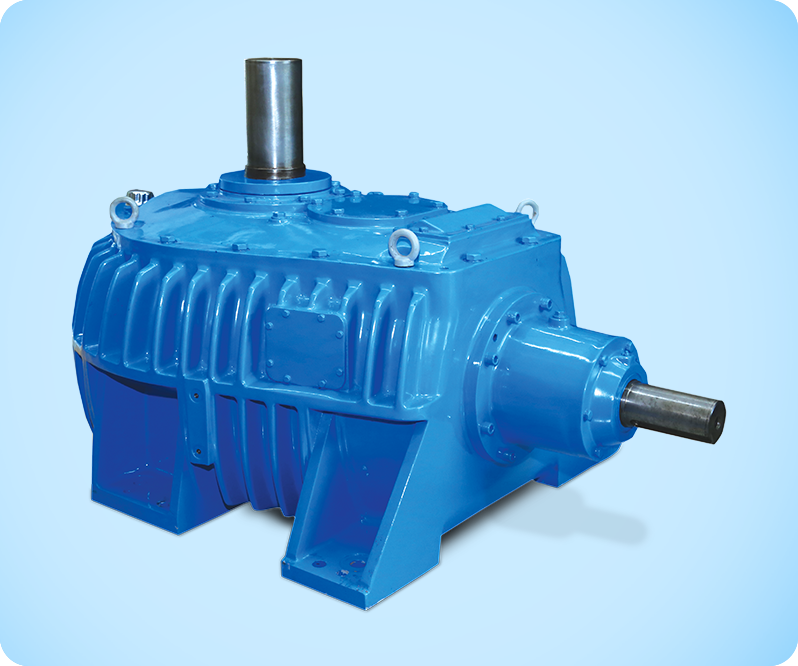
Cooling Tower Gear Reducer
Cooling tower gear reducers are an essential component of cooling towers. They play a critical role in the efficient and effective operation of the tower, ensuring that it can coolwater efficiently while reducing energy consumption. In this blog post, we will take a closer look at cooling tower gear reducers, their functions, benefits, and types.
Functions of Cooling Tower Gear Reducers
The primary function of a cooling tower gear reducer is to drive the fan that pulls airthrough the cooling tower. This fan creates a flow of air that cools the water as it passesthrough the tower. The gear reducer is responsible for controlling the speed and torqueof the fan, ensuring that it operates efficiently and effectively.
Benefits of Cooling Tower Gear Reducers
Cooling tower gear reducers offer several benefits over other types of gear reducers. Some of the most significant benefits of cooling tower gear reducers include:
Types of Cooling Tower Gear Reducers
There are several different types of cooling tower gear reducers available on the market. Some of the most common types of cooling tower gear reducers include:
In conclusion, cooling tower gear reducers are a critical component of cooling towers. They are designed to drive the fan that pulls air through the tower, ensuring that it can cool water efficiently while reducing energy consumption. By understanding thefunctions, benefits, and types of cooling tower gear reducers, users can select the righttype of reducer for their specific application, ensuring maximum performance andefficiency.

Bevel Reducer
Bevel reducers are a type of power transmission equipment that are commonly used in various industrial applications. They are designed to transmit power between shafts thatare perpendicular to each other, allowing them to change the direction of powertransmission. In this blog post, we will take a closer look at bevel reducers, theirfunctions, types, and benefits.
Functions of Bevel Reducers
The primary function of a bevel reducer is to transmit power between two shafts thatare perpendicular to each other. This is achieved by using bevel gears that mesh witheach other at an angle, allowing them to transmit power smoothly and efficiently. Theoutput shaft of the reducer is typically slower but has a higher torque than the inputshaft, allowing it to drive heavy loads with ease.
Types of Bevel Reducers
There are several different types of bevel reducers available on the market, eachdesigned for specific applications and operating conditions. Some of the most commontypes of bevel reducers include:
Benefits of Bevel Reducers
Bevel reducers offer several benefits over other types of power transmission equipment. Some of the most significant benefits of bevel reducers include:
In conclusion, bevel reducers are an essential component in various industrialapplications. They are designed to transmit power between two shafts that areperpendicular to each other, allowing them to change the direction of powertransmission. By understanding the functions, types, and benefits of bevel reducers, users can select the right type of reducer for their specific application, ensuringmaximum performance and efficiency.
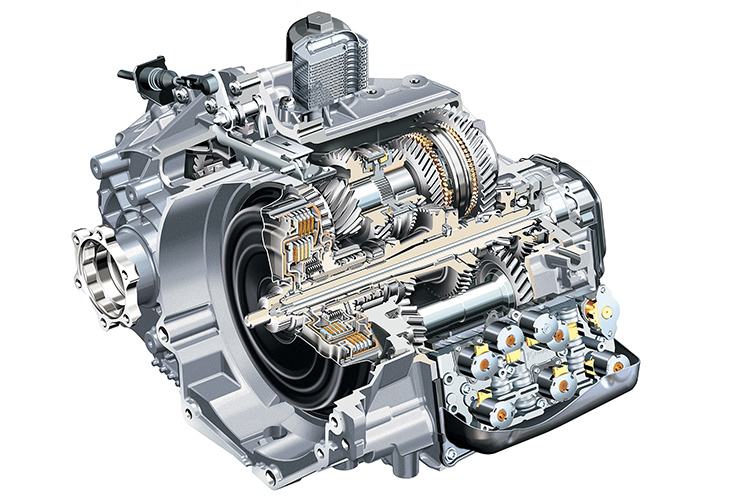
List of Ten Different Types of Industrial Gearboxes
Here are ten different types of industrial gearboxes:
1.Helical Gearbox: This type of gearbox has helical gears, which have teeth thatare cut at an angle to the gear axis. Helical gearboxes are known for their smooth andquiet operation, and they are commonly used in conveyor systems, cranes, and mixers.
2.Planetary Gearbox: This type of gearbox has a central sun gear, planet gears, and a ring gear. Planetary gearboxes are known for their high torque and compactdesign, and they are commonly used in industrial machinery, robotics, and automotiveapplications.
3.Worm Gearbox: This type of gearbox has a worm gear that meshes with a spurgear. Worm gearboxes are known for their high reduction ratio, making them useful in applications that require slow speeds and high torque, such as winches, hoists, andconveyors.
4.Bevel Gearbox: This type of gearbox has bevel gears that are used to transmit power between shafts that are not parallel. Bevel gearboxes are commonly used in industrial applications that require high speed and efficiency, such as pumps, compressors, and turbines.
5.Cycloidal Gearbox: This type of gearbox uses a set of cycloidal disks to transmit power between shafts. Cycloidal gearboxes are known for their high torque and lowbacklash, and they are commonly used in industrial machinery, robotics, andautomation applications.
6.Parallel Shaft Gearbox: This type of gearbox has parallel shafts that transmit power between gears. Parallel shaft gearboxes are commonly used in industrialapplications that require high power transmission, such as steel mills and miningequipment.
7.Offset Shaft Gearbox: This type of gearbox has offset shafts that transmit power between gears. Offset shaft gearboxes are commonly used in industrialapplications that require precise positioning, such as printing presses and packagingmachinery.
8.Right-Angle Gearbox: This type of gearbox has right-angle gears that transmit power between shafts that are perpendicular to each other. Right-angle gearboxes arecommonly used in industrial applications that require compact design and high torque, such as machine tools and robotics.
9.Hypoid Gearbox: This type of gearbox has hypoid gears that are designed totransmit power between non-intersecting shafts. Hypoid gearboxes are commonly usedin automotive applications, such as differential gears.
10.Harmonic Drive Gearbox: This type of gearbox uses a set of flexspline, wavegenerator, and circular spline to transmit power with high precision and low backlash. Harmonic drive gearboxes are commonly used in industrial robots, semiconductorequipment, and aerospace applications.
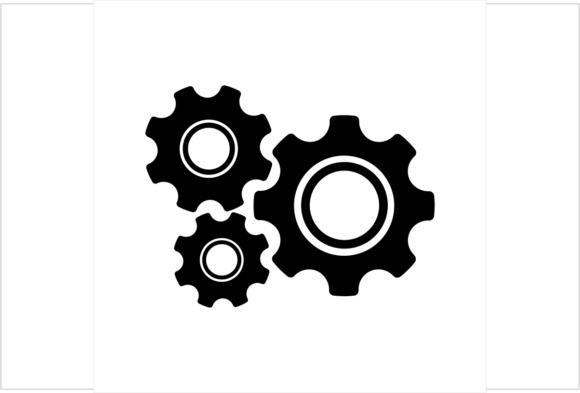
Types of Gear and Their Features
Types of Gear Types and Their Features
Here are 25 types of gears with brief descriptions of their features:
1.Spur Gears: Simplest and most common type of gear, with straight teeth that are parallel to the axis of rotation.
2.Helical Gears: Similar to spur gears, but with teeth that are angled or helical, which makes them quieter and smoother in operation.
3.Double Helical Gears: Also known as herringbone gears, they have two sets of teeth that are angled in opposite directions to cancel out axial forces.
4.Bevel Gears: Used to transmit power and motion between shafts that are at an angle to each other, with cone-shaped teeth.
5.Hypoid Gears: Similar to bevel gears, but with non-intersecting axes, which allows for a larger gear ratio.
6.Worm Gears: Consist of a worm gear and worm wheel, used for high reduction ratios and a right-angle drive.
7.Rack and Pinion Gears: Used to convert rotational motion into linear motion, with a linear rack and a circular pinion.
8.Spur Rack Gears: Straight-toothed gears that are linear in shape and used for linear motion.
9.Internal Gears: Similar to spur gears but with teeth on the inside, used for planetary gear systems.
10.Planetary Gears: Consist of a central sun gear, planet gears, and a ring gear, used for high torque and compact design.
11.Epicyclic Gears: Similar to planetary gears, but with more complex motion paths and greater flexibility in design.
12.Straight Bevel Gears: Similar to bevel gears, but with teeth that are straight rather than curved.
13.Spiral Bevel Gears: Similar to straight bevel gears, but with angled teeth for smoother operation and greater load capacity.
14.Zerol Bevel Gears: A type of spiral bevel gear with teeth that are curved in both the axial and radial directions.
15.Crown Gears: Used in differential systems, with cylindrical teeth that are perpendicular to the axis of rotation.
16.Face Gears: Similar to crown gears, but with teeth that are flat and perpendicular to the axis of rotation.
17.Skew Bevel Gears: A type of bevel gear with teeth that are angled in both the axial and radial directions.
18.Hypocycloid Gears: A type of planetary gear that has a smaller diameter than the sun gear.
19.Cycloid Gears: Similar to hypocycloid gears, but with a more complex shape and greater flexibility in design.
20.Spiroid Gears: A type of spiral bevel gear with a more complex tooth shape and greater load capacity.
21.Coniflex Gears: Similar to spiral bevel gears, but with a different tooth shape that allows for smoother operation and greater load capacity.
22.Involute Gears: A type of spur gear with teeth that have a specific profile shape for smoother operation.
23.Quick-Change Gears: Used in machine tools for quick and easy gear changes.
24.Variable Speed Gears: Used to vary the speed of a machine or device, with adjustable gear ratios.
25.Continuously Variable Transmissions (CVTs): Use a belt or chain that can vary in width to achieve an infinite number of gear ratios.
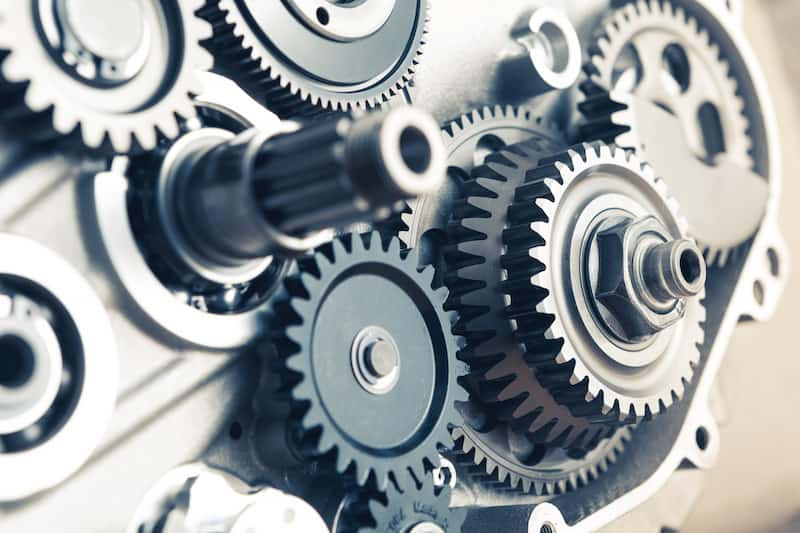
Gear
A gear is a rotating mechanical component with teeth or cogs that mesh with anothergear to transmit power and motion. They are used in a wide variety of machines anddevices to change the speed, torque, and direction of motion.
There are several types of gears, each with its own specific design and function. Here aresome of the most common types of gears:
1.Spur Gears: Spur gears are the simplest and most common type of gear. They have straight teeth that are arranged in a parallel fashion along the gear’s axis. They areused in a wide variety of applications, including cars, clocks, and industrial machinery.
2.Helical Gears: Helical gears are similar to spur gears but have angled teeth thatare arranged in a helix pattern along the gear’s axis. This design reduces noise andimproves smoothness in operation. Helical gears are commonly used in car transmissions and industrial machinery.
3.Bevel Gears: Bevel gears have cone-shaped teeth that allow them to transmit power and motion between two shafts that are at an angle to each other. They are usedin many applications, including power tools, vehicles, and industrial machinery.
4.Worm Gears: Worm gears consist of a worm or screw gear that meshes with a worm wheel. They are used to transmit motion at a right angle and are commonly foundin steering systems, elevators, and industrial machinery.
5.Rack and Pinion Gears: Rack and pinion gears consist of a straight bar (therack) with teeth that mesh with a small gear (the pinion). They are commonly used in steering systems and can convert rotational motion into linear motion.
6.Planetary Gears: Planetary gears consist of a sun gear, planet gears, and a ring gear. They are used in many applications, including car transmissions, industrialmachinery, and robotics.
Overall, gears are essential components in many machines and devices, and the type of gear used depends on the specific application and requirements of the machine or device.

Worm Gear
Worm gears are a type of gear system commonly used in mechanical powertransmissions to achieve high gear reduction ratios. These gears consist of a worm, which is a cylindrical screw-like shaft, and a worm wheel, which is a gear with helicalteeth that mesh with the worm. In this blog post, we will explore the benefits andapplications of worm gears.
Advantages of Worm Gears
Applications of Worm Gears
Conclusion
Worm gears are a versatile and reliable type of gear system that can achieve high gearreduction ratios, are self-locking, and have a compact size. These features make themsuitable for a wide range of applications, including the automotive industry, materialhandling, food processing, and construction equipment. With their smooth operationand reliable performance, worm gears are an essential component of many mechanicalsystems.

Timing Pulleys
Timing pulleys are an essential component in many mechanical systems. They are usedto transfer power and motion between rotating shafts, and they play a critical role in ensuring that these systems operate efficiently and effectively. In this blog post, we willtake a closer look at timing pulleys, their functions, types, and benefits.
Functions of Timing Pulleys
The primary function of a timing pulley is to transfer rotational motion and power fromone shaft to another. They do this by means of teeth or grooves on their surface, whichinterlock with teeth or grooves on a mating belt or chain. Timing pulleys are designed tomaintain a constant rotational speed, ensuring that the driven shaft rotates at the samespeed as the driving shaft.
Types of Timing Pulleys
There are several different types of timing pulleys available on the market, eachdesigned for specific applications and operating conditions. Some of the most commontypes of timing pulleys include:
Benefits of Timing Pulleys
Timing pulleys offer several benefits over other types of power transmissioncomponents. Some of the most significant benefits of timing pulleys include: