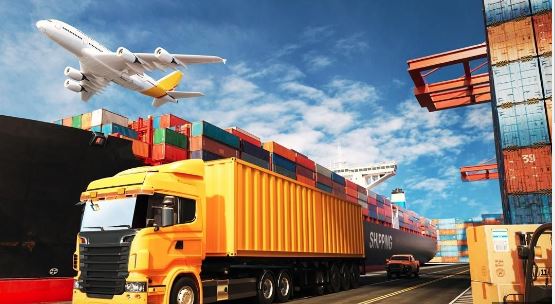
The Significance of Gears and Gearboxes in the Transportation Industry
The transportation industry plays a vital role in the global economy, connecting people and goods across various modes of transport. Within this industry, gears and gearboxes are essential components that enable the efficient and reliable operation of vehicles. Whether it’s cars, trucks, trains, or ships, gears and gearboxes are utilized to transmit power, control speed, and enhance overall performance. In this blog post, we will explore the importance of gears and gearboxes in the transportation industry.
1. Power Transmission: Gears and gearboxes are key elements in power transmission within vehicles. They are responsible for transferring power from the engine to the wheels or propellers, enabling movement and propulsion. By utilizing different gear ratios, gears and gearboxes allow vehicles to optimize power delivery based on specific requirements, such as acceleration, towing capacity, or fuel efficiency. Efficient power transmission ensures that vehicles can operate smoothly and effectively, regardless of the mode of transportation.
2. Speed Control: Controlling speed is crucial in transportation to ensure safety and efficiency. Gears and gearboxes enable speed control by offering various gear ratios. By changing gears, vehicles can achieve different speeds based on road conditions, terrain, or desired performance. Gearboxes provide the flexibility to adapt to different driving or operating conditions, allowing vehicles to operate efficiently across a wide range of speed requirements. This versatility is particularly important in applications such as heavy-duty trucks, where the ability to handle different load capacities and gradients is necessary.
3. Torque Conversion: Gears and gearboxes also facilitate torque conversion in transportation vehicles. Torque is the rotational force generated by the engine, and it needs to be appropriately converted to achieve the desired output. Through gear systems, gears and gearboxes can increase or decrease torque to match the vehicle’s requirements. This is particularly relevant in applications such as towing, where high torque is necessary to overcome resistance or inclines. Gearboxes allow vehicles to effectively convert engine torque into usable power, ensuring optimal performance and efficiency.
4. Durability and Load Handling: Transportation vehicles often operate under demanding conditions, such as carrying heavy loads or enduring challenging terrains. Gears and gearboxes play a crucial role in ensuring durability and load handling capabilities. They are designed to withstand high stress and distribute the load evenly across the drivetrain. By effectively distributing the forces exerted on the vehicle’s components, gears and gearboxes help minimize wear and tear, extend the lifespan of the vehicle, and enhance overall reliability.
5. Efficiency and Fuel Economy: In an era of increasing environmental awareness, efficiency and fuel economy are paramount in the transportation industry. Gears and gearboxes contribute significantly to achieving these goals. By optimizing power delivery and controlling speed, vehicles can operate at their most efficient RPM range. Gearboxes enable vehicles to maintain optimal engine speed and torque, resulting in improved fuel efficiency. Efficient power transmission through gears and gearboxes ensures that the vehicle’s engine operates in its sweet spot, maximizing performance while minimizing fuel consumption.
Gears and gearboxes play a crucial role in the transportation industry by enabling power transmission, speed control, torque conversion, durability, and fuel efficiency. Whether it’s cars, trucks, trains, or ships, these components are essential for reliable and efficient vehicle operation. As the transportation industry continues to evolve, the advancements in gear and gearbox technology will further enhance performance, sustainability, and safety, driving us towards a more connected and sustainable future.
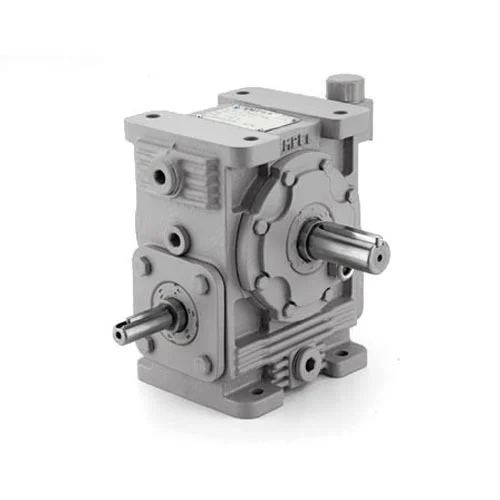
Worm Reducers
Worm reducers are an essential component in many industrial applications where hightorque and slow speed are required. They are commonly used in conveyor systems, manufacturing equipment, and heavy-duty machinery. In this blog post, we’ll explorethe features and benefits of worm reducers.
Features of Worm Reducers
Worm reducers consist of a worm gear and a worm wheel. The worm gear is a screw-shaped component that meshes with the worm wheel, which is a cylindrical gear. Theworm gear’s rotation causes the worm wheel to rotate at a slower speed whilemaintaining the same torque output.
One of the key features of worm reducers is their ability to handle high torque loads. This is because the worm gear and worm wheel mesh at an angle, which allows them totransmit power with a high torque output. Additionally, worm reducers have a highreduction ratio, which allows for a slow output speed, making them ideal forapplications where precise control is required.
Worm reducers are also known for their compact design, which allows them to be installed in tight spaces. They are typically made of durable materials such as steel orcast iron to withstand the high loads and harsh environments commonly found in industrial applications.
Benefits of Worm Reducers
There are several benefits to using worm reducers in industrial applications. Some of these benefits include:
Conclusion
In conclusion, worm reducers are an important component in many industrialapplications due to their ability to handle high torque loads and provide precise controlover power transmission. Their compact design, low noise operation, high efficiency, smooth operation, and customizability make them a popular choice for heavy-dutymachinery. By using worm reducers, businesses can improve their productivity andreduce their operating costs, making them a wise investment for any industrialapplication.
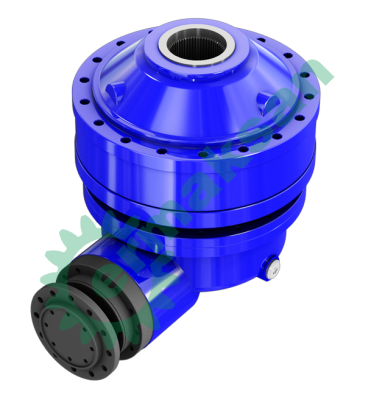
Twin Shaft Reducers
Twin shaft reducers are an essential component in many industrial applications. They are used to reduce the speed of a motor or engine to the desired output speed. This typeof reducer is especially useful in applications where high torque is required, such as conveyor systems or heavy-duty machinery. In this blog post, we will explore thefeatures and benefits of twin shaft reducers.
Features of Twin Shaft Reducers
Twin shaft reducers consist of two parallel shafts with gears that mesh together toreduce the input speed. The gears are usually made of high-strength materials such as hardened steel or cast iron to handle the high torque loads. The two shafts rotate in opposite directions to maintain balance and prevent excessive wear and tear.
Another feature of twin shaft reducers is their compact design. They can be installed in tight spaces without compromising their efficiency or durability. This is important forapplications where space is limited, such as in mining or manufacturing facilities.
Benefits of Twin Shaft Reducers
There are several benefits to using twin shaft reducers in industrial applications. Someof these include:
Conclusion
Twin shaft reducers are a vital component in many industrial applications, providingreliable and efficient power transmission. Their high torque capacity, low maintenancerequirements, energy efficiency, smooth operation, and customizability make them a popular choice for heavy-duty machinery. By using twin shaft reducers, businesses can improve their productivity and reduce their operating costs, making them a wiseinvestment for any industrial application.

Swing Reducers
Swing reducers, also known as swing drives, are an essential component in manyconstruction and heavy equipment applications. They are used to control the rotationalmovement of the machine’s upper structure, such as the cab or boom, allowing forprecise control over the equipment’s movement. In this blog post, we’ll explore thefeatures and benefits of swing reducers.
Features of Swing Reducers
Swing reducers consist of a gearbox that is mounted to the machine’s frame and a hydraulic motor that drives the gearbox. The gearbox’s output shaft is connected to theupper structure, allowing it to rotate in either direction.
The gearbox is typically made of high-strength materials such as steel to withstand thehigh loads and harsh environments commonly found in construction and heavyequipment applications. The hydraulic motor is also designed to handle high torqueloads and provide precise control over the rotational movement of the upper structure.
Swing reducers are available in a range of sizes and torque capacities to match therequirements of the equipment they are installed on. They can also be customized toinclude additional features such as brake systems to provide additional control over themachine’s movement.
Benefits of Swing Reducers
There are several benefits to using swing reducers in construction and heavy equipmentapplications. Some of these benefits include:
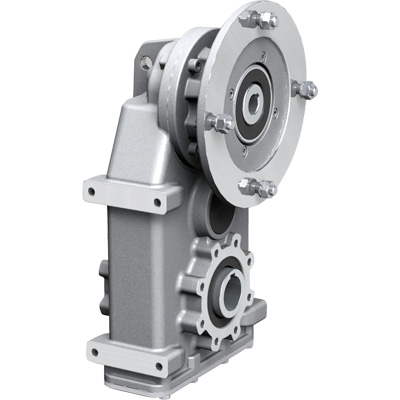
Shaft-Mounted Helical Gearboxes
Shaft-mounted helical gearboxes are a type of power transmission equipment that arecommonly used in various industrial applications. They are designed to transmit powerbetween a motor and a driven machine, allowing them to operate efficiently andeffectively. In this blog post, we will take a closer look at shaft-mounted helicalgearboxes, their functions, types, and benefits.
Functions of Shaft-Mounted Helical Gearboxes
The primary function of a shaft-mounted helical gearbox is to transmit power between a motor and a driven machine. This is achieved by using helical gears that mesh with eachother, allowing them to transmit power smoothly and efficiently. The gearbox is mounted directly onto the shaft of the driven machine, eliminating the need for a separate coupling or foundation.
Benefits of Shaft-Mounted Helical Gearboxes
Shaft-mounted helical gearboxes offer several benefits over other types of powertransmission equipment. Some of the most significant benefits of shaft-mounted helicalgearboxes include:
Types of Shaft-Mounted Helical Gearboxes
There are several different types of shaft-mounted helical gearboxes available on themarket, each designed for specific applications and operating conditions. Some of themost common types of shaft-mounted helical gearboxes include:
In conclusion, shaft-mounted helical gearboxes are an essential component in variousindustrial applications. They are designed to transmit power between a motor and a driven machine, allowing them to operate efficiently and effectively. By understandingthe functions, types, and benefits of shaft-mounted helical gearboxes, users can select theright type of gearbox for their specific application, ensuring maximum performance andefficiency.

Rolling Mill Gearboxes
Rolling mill gearboxes play a vital role in the steel production process, as they help totransmit power and torque from the main motor to the rolling mill. These gearboxes arecritical components in the steel manufacturing process, and their reliability andperformance can have a significant impact on the overall production efficiency andprofitability of a steel mill.
In this blog post, we will take a closer look at rolling mill gearboxes, their functions, types, and maintenance practices.
Functions of Rolling Mill Gearboxes
The primary function of a rolling mill gearbox is to transmit power and torque from themain motor to the rolling mill. The gearbox also provides speed reduction and torquemultiplication, which helps to increase the force applied to the steel being rolled. Rolling mill gearboxes must be able to handle high torque and heavy loads, and they must be designed to withstand the harsh operating conditions of a steel mill.
Types of Rolling Mill Gearboxes
There are several different types of rolling mill gearboxes, each designed for specificapplications and operating conditions. Some of the most common types of rolling millgearboxes include:
Maintenance Practices for Rolling Mill Gearboxes
Proper maintenance is essential for ensuring the reliability and performance of rollingmill gearboxes. Some of the most important maintenance practices for rolling millgearboxes include:
In conclusion, rolling mill gearboxes are critical components in the steel manufacturingprocess. They play a vital role in transmitting power and torque from the main motor tothe rolling mill, and their reliability and performance can have a significant impact on the overall production efficiency and profitability of a steel mill. By understanding thefunctions, types, and maintenance practices of rolling mill gearboxes, steel mills can ensure that their gearboxes are operating at peak performance and reliability.
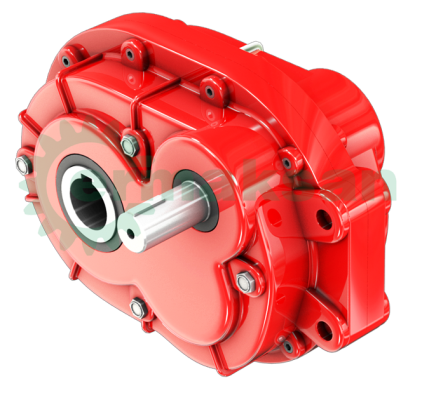
Reducer Conveyor Belts
In many industrial applications, conveyor belts play a crucial role in the efficient andsafe transportation of materials. However, conveyor belts can operate at high speeds, making it challenging to control the flow of materials in some cases. That’s wherereducer conveyor belts come in. In this blog post, we’ll explore the features and benefitsof reducer conveyor belts.
Features of Reducer Conveyor Belts
A reducer conveyor belt is designed with a specialized gearbox that reduces the speed of the conveyor belt while maintaining the same torque. The gearbox is typically mounteddirectly onto the drive pulley of the conveyor belt and works by converting the high-speed rotational motion of the motor or engine into a lower speed but higher torqueoutput.
The reducer conveyor belt consists of a series of gears and bearings that are designed towithstand high loads and work efficiently in harsh environments. The gears are typicallymade of high-strength materials such as hardened steel or cast iron to handle the hightorque loads generated by the conveyor belt.
Benefits of Reducer Conveyor Belts
There are several benefits to using a reducer conveyor belt in industrial applications. Some of these benefits include:
Conclusion
In conclusion, reducer conveyor belts play an important role in many industrialapplications by improving the safety, efficiency, and control of conveyor systems. Theirability to reduce the speed of the conveyor belt while maintaining the same torqueoutput provides many benefits, including increased safety, improved efficiency, bettercontrol, longer belt life, and customizability. If you’re looking to improve your conveyorsystem’s performance, a reducer conveyor belt may be the solution you need.
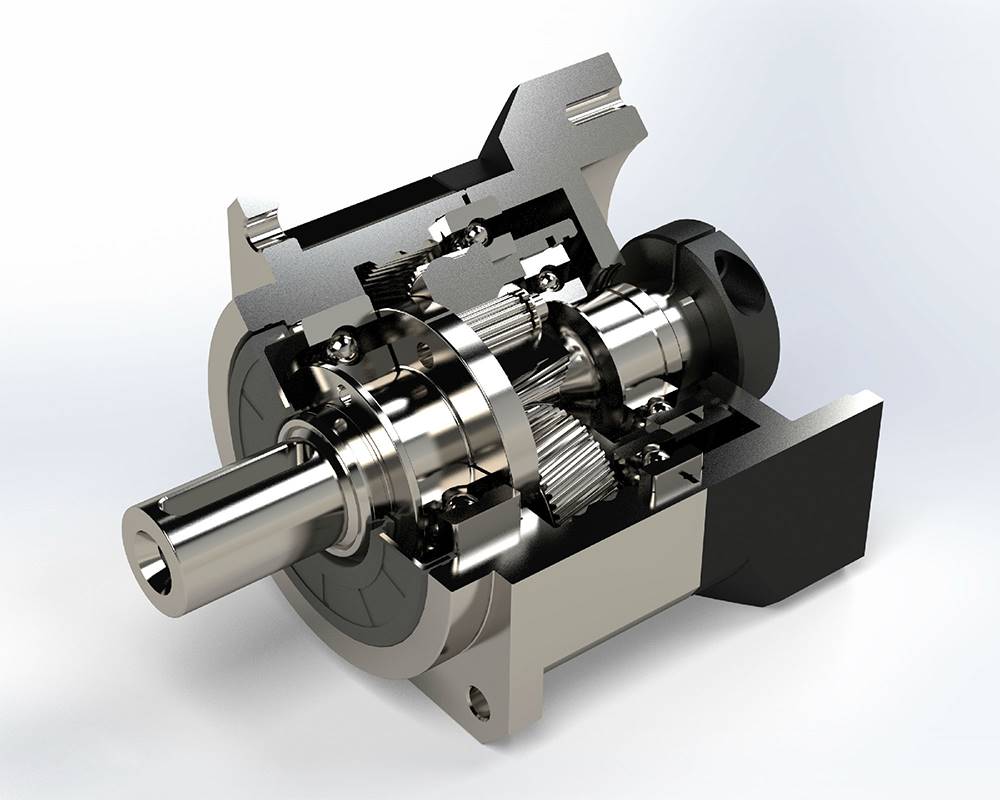
Planetary Gearheads
Planetary gearheads are an essential component in many mechanical systems, particularly those requiring high precision, torque, and speed control. These gearheadsare commonly used in industrial automation, robotics, medical equipment, and otherapplications that require precise motion control. In this blog post, we will take a closerlook at planetary gearheads, how they work, their advantages, and their applications.
How Planetary Gearheads Work:
Planetary gearheads work by using a system of gears that rotate around a central sun gear. The sun gear is typically connected to the motor, while the planet gears rotatearound it, driven by an outer ring gear. The configuration of these gears allows for a range of gear ratios, providing precise control over the speed and torque of the outputshaft.
Planetary gearheads are designed for high precision and accuracy, with minimal backlash and smooth operation. They are also able to handle high torque loads, makingthem ideal for applications where high torque is required at low speeds.
Advantages of Planetary Gearheads:
Planetary gearheads offer several advantages over other types of gearheads, including:
Applications of Planetary Gearheads:
Planetary gearheads are used in a wide variety of applications, including:
Conclusion:
Planetary gearheads are an essential component in many mechanical systems, providinghigh precision, torque, and speed control. They work by using a system of gears thatrotate around a central sun gear, providing a range of gear ratios for precise motioncontrol. Planetary gearheads offer several advantages over other types of gearheads, including high precision, high torque, compact size, low noise, and high efficiency. They are used in a wide variety of applications, including industrial automation, medicalequipment, aerospace, and automotive. With their ability to provide precise motioncontrol and handle high torque loads, planetary gearheads are a critical component in many mechanical systems.
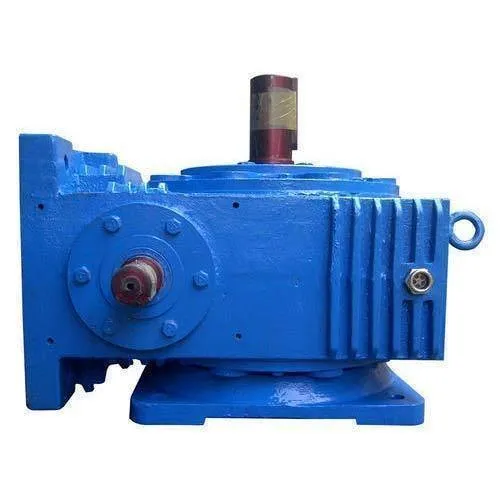
Pan Mixer Reducer
Pan mixer reducers, also known as pan mixer gearboxes, are a crucial component in theconstruction industry. They are designed to mix different types of constructionmaterials, including concrete, mortar, and plaster, to create a homogenous mixture thatcan be used for construction projects. In this blog post, we will take a closer look at panmixer reducers, their function, features, and benefits.
Function of Pan Mixer Reducers:
Pan mixer reducers are designed to mix different types of construction materials, ensuring a uniform and consistent mixture. They work by receiving power from an electric motor, which is transmitted to the gearbox. The gearbox then reduces the speedof the motor and increases the torque to mix the construction materials thoroughly.
Features of Pan Mixer Reducers:
Pan mixer reducers come with a range of features, including:
Benefits of Pan Mixer Reducers:
Pan mixer reducers offer several benefits to the construction industry, including:
Applications of Pan Mixer Reducers:
Pan mixer reducers are used in a variety of construction applications, including:
Conclusion:
Pan mixer reducers are a critical component in the construction industry, ensuring a uniform and consistent mixture of different construction materials. They offer severalbenefits, including improved mixing quality, increased efficiency, reduced labor costs, and greater flexibility. With their high-quality materials, compact design, andcustomization options, pan mixer reducers are an ideal solution for the constructionindustry. They are used in concrete mixing, mortar mixing, and plaster mixingapplications, ensuring that construction materials are of high quality and uniformconsistency.
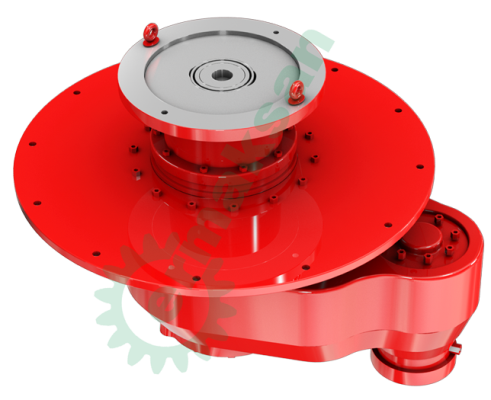
Octopus Mixer Type Reducers
Octopus mixer type reducers are a type of gear reducer that is commonly used in industrial mixing applications. They are designed to provide high torque and low-speedoutput to mix materials in a precise and efficient manner. In this blog post, we’ll explorethe features and benefits of octopus mixer type reducers.
Features of Octopus Mixer Type Reducers
Octopus mixer type reducers consist of a gearbox with several shafts that are arrangedin a circular pattern, similar to the legs of an octopus. Each shaft is connected to a mixing blade, which rotates around the central axis of the gearbox.
The gearbox is typically made of high-strength materials such as cast iron or steel towithstand the high torque loads generated during the mixing process. The shafts andblades are also made of durable materials to handle the abrasive nature of many mixingapplications.
Octopus mixer type reducers are available in a range of sizes and torque capacities tomatch the requirements of the mixing application. They can also be customized toinclude additional features such as heating or cooling elements to maintain a consistenttemperature during the mixing process.
Benefits of Octopus Mixer Type Reducers
There are several benefits to using octopus mixer type reducers in industrial mixingapplications. Some of these benefits include:
Conclusion
In conclusion, octopus mixer type reducers are a versatile and reliable solution for manyindustrial mixing applications. Their high torque capacity, precise mixing capabilities, low speed output, durability, and customizability make them an ideal investment forbusinesses looking to improve their mixing processes. By using octopus mixer typereducers, businesses can increase their productivity and efficiency, while also improvingthe quality of their products.