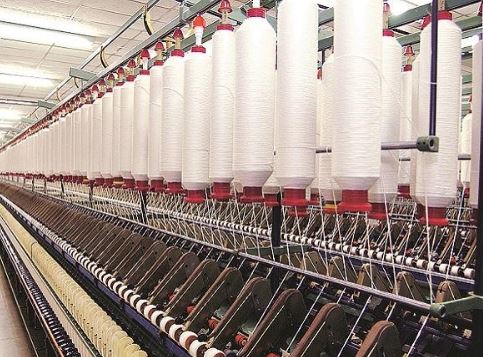
The Role of Gears and Gearboxes in the Textile Industry
The textile industry is a dynamic sector that involves the manufacturing of fibers, fabrics, and various textile products. Within this industry, gears and gearboxes are essential components used in textile machinery to facilitate efficient production processes. Gears enable the transmission of power and motion, while gearboxes provide speed control and torque conversion. In this blog post, we will explore the significance of gears and gearboxes in the textile industry.
1. Power Transmission: Gears and gearboxes play a crucial role in power transmission within textile machinery. From spinning machines to weaving looms, gears are responsible for transmitting power from the motor to various components, such as spindles, rollers, and shafts. They ensure that the necessary rotational motion is efficiently transferred to drive the production process. Gears help maintain consistent speed and torque, resulting in uniform and high-quality textile output.
2. Speed Control: Speed control is vital in textile manufacturing to achieve desired results and maintain product quality. Gears and gearboxes enable speed control by providing different gear ratios. By changing gears, textile machinery can operate at various speeds, accommodating different fabric types, yarn thicknesses, and production requirements. Gearboxes allow operators to adjust the rotational speed of critical components, ensuring precise control over the manufacturing process.
3. Torque Conversion: Textile machinery often requires torque conversion to handle different types of fabrics and manufacturing stages. Gears and gearboxes facilitate torque conversion by adjusting the rotational force transmitted to the components. They allow textile machines to generate the appropriate level of torque for specific tasks, such as yarn winding, fabric stretching, or thread tensioning. The ability to convert torque efficiently enhances the overall performance and productivity of textile machinery.
4. Durability and Reliability: Textile manufacturing involves repetitive and demanding operations, subjecting machinery to significant stress and wear. Gears and gearboxes designed for the textile industry are built to withstand these challenging conditions. They are manufactured with high-quality materials and precision engineering to ensure durability and reliability. Proper lubrication and maintenance of gears and gearboxes contribute to extending their lifespan and minimizing downtime in the production process.
5. Customization and Specialized Applications: The textile industry encompasses a wide range of processes and applications, each with its unique requirements. Gears and gearboxes can be customized to meet specific needs, such as different gear profiles, sizes, or materials. This flexibility allows textile manufacturers to optimize their machinery for specialized applications, such as knitting, dyeing, or fabric finishing. Customized gears and gearboxes ensure precise control, efficiency, and consistency throughout the textile production cycle.
Gears and gearboxes are indispensable components in the textile industry, enabling power transmission, speed control, torque conversion, durability, and reliability in textile machinery. Their role in facilitating efficient production processes and maintaining product quality cannot be overstated. As the textile industry continues to evolve, advancements in gear and gearbox technology will further enhance productivity, customization, and sustainability, contributing to the growth and innovation of this dynamic sector.
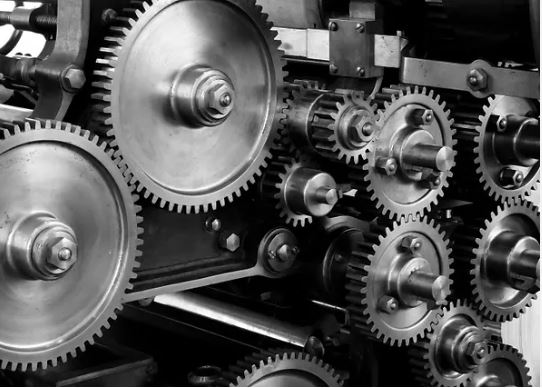
Industrial Gear Market Forecast: Trends, Growth, and Outlook
The industrial gear market is a dynamic sector driven by various industries such as automotive, aerospace, machinery, and energy. Gears play a crucial role in power transmission, motion control, and mechanical systems, making them essential components for industrial applications. In this blog post, we will explore the forecast for the industrial gear market, including key trends, growth factors, and the overall outlook.
Market Size and Growth:
The industrial gear market has been experiencing steady growth over the years, driven by factors such as increasing industrialization, automation, and the need for efficient power transmission systems.
Technological Advancements:
Technological advancements have significantly influenced the industrial gear market. Manufacturers are adopting advanced materials, such as composites and high-performance alloys, to enhance gear performance, durability, and efficiency. Additionally, the integration of smart technologies and the Internet of Things (IoT) in gear systems enable real-time monitoring, predictive maintenance, and improved overall system performance.
Demand from End-Use Industries:
The demand for industrial gears is driven by various end-use industries. The automotive sector, in particular, is a significant consumer of gears for applications such as transmissions, differentials, and steering systems. The aerospace industry also contributes to the growth of the gear market, primarily for aircraft engines and landing gear systems. Other sectors, including machinery, energy, and robotics, also rely on gears for their operations.
Focus on Efficiency and Sustainability:
With increasing emphasis on energy efficiency and sustainability, the industrial gear market is witnessing a shift towards gear designs that reduce friction, enhance efficiency, and minimize energy consumption. Manufacturers are exploring advanced lubrication techniques, surface treatments, and gear geometries to improve overall gear performance and reduce environmental impact.
Regional Outlook:
The industrial gear market’s growth is influenced by different regions around the world. Developing economies, such as China, India, and Southeast Asian countries, are experiencing rapid industrialization and urbanization, driving the demand for industrial gears. North America and Europe, with their established manufacturing industries, also contribute significantly to the market. Additionally, emerging markets in Latin America and the Middle East are projected to present growth opportunities for the industrial gear market.
The industrial gear market is expected to witness steady growth in the coming years, driven by increasing industrialization, technological advancements, and the demand for efficient power transmission systems. The adoption of advanced materials, smart technologies, and a focus on energy efficiency are shaping the future of the gear market. With the continued growth of various end-use industries and the development of emerging markets, the industrial gear market presents promising opportunities for manufacturers and suppliers worldwide.
Please note that the specific forecasted growth rates and market figures mentioned in this blog post are fictional and provided only for illustrative purposes. Actual market data may vary and should be obtained from reliable sources and market research reports.
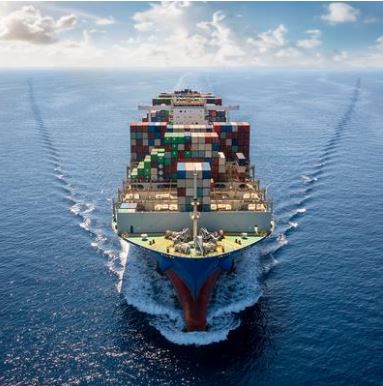
The Importance of Gears and Gearboxes in the Maritime Industry
The maritime industry plays a crucial role in global trade and transportation, with ships and vessels being the backbone of international commerce. Within this industry, gears and gearboxes are integral components that enable the efficient and reliable operation of maritime machinery and propulsion systems. Gears facilitate power transmission and motion control, while gearboxes provide speed adjustment and torque conversion. In this blog post, we will explore the significance of gears and gearboxes in the maritime industry.
1. Propulsion System: Gears and gearboxes are fundamental to the propulsion systems of ships and vessels. They play a critical role in transferring power from the engines to the propellers, enabling the vessel to move through the water. Gears ensure that the rotational motion produced by the engines is efficiently transmitted to the propellers, generating thrust and propulsion. Gearboxes allow for speed adjustment, allowing ships to operate optimally at various speeds based on specific requirements such as cruising, maneuvering, or docking.
2. Power Generation: In addition to propulsion, gears and gearboxes are used in power generation systems on maritime vessels. Many ships are equipped with auxiliary engines and generators to provide electrical power for various onboard systems. Gears and gearboxes facilitate power transmission from the engines to the generators, ensuring a reliable and efficient supply of electricity. They allow for speed control and torque conversion, optimizing the operation of the power generation systems.
3. Steering and Maneuvering: Gears and gearboxes are also crucial in the steering and maneuvering systems of maritime vessels. Rudder systems, thrusters, and other control surfaces rely on gears to transmit motion and provide precise control. Gearboxes allow for the adjustment of the rotational speed and torque, enabling effective steering and maneuvering of the vessel. The accurate and responsive operation of these systems ensures safe navigation, especially in congested waters or challenging maritime conditions.
4. Load Handling and Cargo Operations: Maritime vessels often handle heavy loads and cargo, requiring robust and reliable equipment for load handling operations. Gears and gearboxes are utilized in cranes, winches, and cargo handling systems to facilitate efficient and controlled movement of cargo. They provide the necessary torque conversion and power transmission to handle diverse cargo requirements, contributing to safe and efficient loading and unloading operations.
5. Durability and Reliability: The maritime industry operates in harsh and demanding environments, including saltwater corrosion, extreme temperatures, and high loads. Gears and gearboxes used in maritime applications are designed to withstand these challenging conditions. They are built with durable materials, precision engineering, and robust construction to ensure reliability and longevity. Proper lubrication and maintenance of gears and gearboxes are essential to ensure their performance and minimize downtime in maritime operations.
Gears and gearboxes are critical components in the maritime industry, enabling power transmission, speed control, maneuverability, and cargo handling capabilities of ships and vessels. Their presence in propulsion systems, power generation systems, and steering mechanisms ensures safe and efficient maritime operations. As the maritime industry continues to evolve, advancements in gear and gearbox technology will further enhance efficiency, sustainability, and safety, contributing to the growth and development of this vital sector of the global economy.
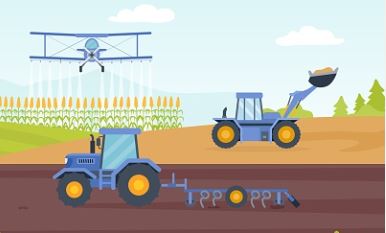
The Role of Gears and Gearboxes in Tractors, Agricultural Machinery, and Irrigation Systems
Tractors, agricultural machinery, and irrigation systems are integral to modern farming practices. Within these applications, gears and gearboxes play a crucial role in power transmission, control, and efficiency. Gears facilitate power transfer and motion control, while gearboxes provide speed adjustment and torque conversion. In this blog post, we will explore the significance of gears and gearboxes in tractors, agricultural machinery, and irrigation systems.
1. Tractors: Tractors are the backbone of agricultural operations, providing power and mobility for various tasks. Gears and gearboxes are essential components in tractors, enabling power transmission and control. They facilitate the transfer of power from the engine to the wheels or the power take-off (PTO) shaft, allowing for efficient traction and the operation of various implements such as plows, harrows, and mowers. Gearboxes provide speed adjustment, allowing operators to optimize tractor speed based on the specific task and terrain conditions.
2. Agricultural Machinery: Agricultural machinery encompasses a wide range of equipment used in farming operations. Gears and gearboxes are employed in various agricultural machines to facilitate power transmission and control. For example, in harvesters and combines, gears and gearboxes enable the movement of cutting blades, conveyor belts, and grain handling systems, ensuring efficient harvesting and processing. In seeders and planters, gears and gearboxes control the distribution of seeds or fertilizers, optimizing the planting process.
3. Irrigation Systems: Irrigation is crucial for agricultural productivity, and gears and gearboxes play a role in irrigation systems. They facilitate power transmission and control in water pumps, allowing for efficient water delivery to crops. Gearboxes provide speed adjustment, enabling operators to control pump speed and optimize water flow rates based on irrigation needs. Gears and gearboxes also play a role in controlling irrigation valves and sprinkler systems, ensuring precise water distribution and coverage.
4. Speed Control and Efficiency: Gears and gearboxes offer speed control capabilities, which are essential for optimal performance and efficiency in agricultural operations. They allow operators to adjust the speed of implements or attachments, ensuring the appropriate operating speed for specific tasks. By optimizing speed, gears and gearboxes contribute to improved efficiency, reduced fuel consumption, and enhanced overall productivity in farming operations.
5. Durability and Reliability: Gears and gearboxes used in tractors, agricultural machinery, and irrigation systems are designed to withstand demanding conditions. They are constructed with durable materials and precise engineering to ensure reliability and longevity. Regular maintenance and lubrication of gears and gearboxes are crucial to minimize wear and tear, ensuring optimal performance and extending their lifespan.
Gears and gearboxes are vital components in tractors, agricultural machinery, and irrigation systems, enabling power transmission, control, and efficiency. From tractors providing traction and power to agricultural machines performing various tasks, and irrigation systems delivering water to crops, gears and gearboxes contribute to the productivity and success of farming operations. As technology continues to advance, gears and gearboxes will play an even more significant role in enhancing the performance and sustainability of agricultural practices, driving the agriculture industry towards increased efficiency and productivity.
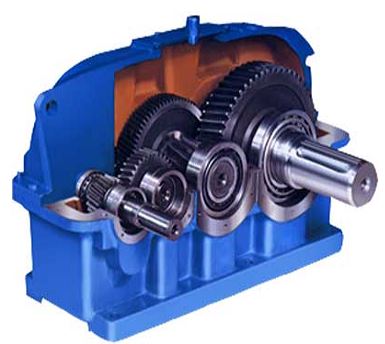
Gearbox Manufacturing Processes: From Design to Production
Gearboxes are critical components used in various industries, including automotive, aerospace, machinery, and robotics. They play a vital role in power transmission and motion control. The manufacturing of gearboxes requires a systematic approach to ensure precision, durability, and reliable performance. In this blog post, we will explore the key steps involved in gearbox manufacturing processes, from design to production.
Gearbox Design:
The first step in gearbox manufacturing is the design phase. Gearbox designers utilize computer-aided design (CAD) software to create detailed 3D models of the gearbox components, including the housing, shafts, bearings, and gears. The design process involves determining the gear ratio, torque requirements, input and output speeds, and the overall size and configuration of the gearbox.
Material Selection:
Selecting the appropriate materials for gearbox components is crucial for strength, durability, and performance. Common materials used for gearbox manufacturing include alloy steels, cast iron, aluminum alloys, and various engineering plastics. The material selection is based on factors such as load capacity, operating conditions, temperature, and cost considerations.
Machining and Fabrication:
After the gearbox design is finalized, the manufacturing process begins with machining and fabrication of the gearbox components. This involves processes such as milling, turning, drilling, and grinding to shape the gearbox housing, shafts, and other parts. CNC (Computer Numerical Control) machines are often used to ensure accuracy and consistency in the manufacturing process.
Gear Cutting:
Gear cutting is a critical step in gearbox manufacturing. It involves the production of gears with the desired tooth profiles and specifications. Gear cutting methods such as hobbing, shaping, milling, or broaching are employed to create the gears. The gear cutting process ensures proper gear meshing and efficient power transmission within the gearbox.
Assembly and Fitting:
Once the gearbox components, including the housing, shafts, bearings, and gears, are manufactured, they are assembled and fitted together. This involves precise alignment and fitting of the components to ensure smooth operation and accurate gear meshing. Lubrication systems and seals are also installed during the assembly process to provide proper lubrication and prevent contamination.
Testing and Quality Control:
Gearboxes undergo rigorous testing and quality control measures to ensure their performance and reliability. Functional tests, such as load testing, vibration testing, and endurance testing, are conducted to verify the gearbox’s ability to handle the specified loads and operating conditions. Additionally, quality control inspections, including dimensional checks and surface finish evaluations, are performed to ensure adherence to design specifications and standards.
Final Finishing and Packaging:
After testing and quality control, the gearbox undergoes any required final finishing operations, such as deburring or surface treatment, to improve its appearance and functionality. The gearbox is then properly packaged, ensuring protection during transportation and storage until it reaches the end-user or assembly line.
Gearbox manufacturing is a complex process that requires precision and attention to detail. From gearbox design and material selection to machining, gear cutting, assembly, testing, and final finishing, each step plays a vital role in producing a high-quality and reliable gearbox. By following stringent manufacturing processes and adhering to quality control measures, gearbox manufacturers can deliver products that meet the performance requirements and specifications of various industries.
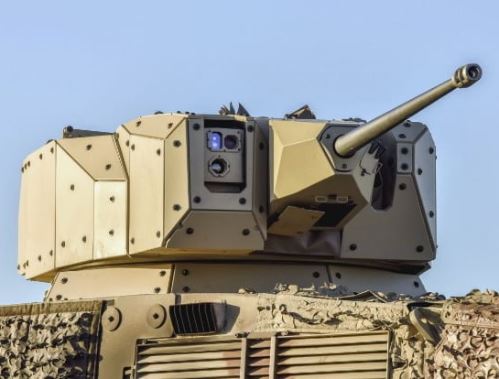
The Role of Gears and Gearboxes in Turret Systems
The Role of Gears and Gearboxes in Turret Systems
Turret systems play a crucial role in various applications, including military vehicles, naval vessels, and defense installations. Within these systems, gears and gearboxes are integral components that enable precise rotation and control of the turret. Gears facilitate power transmission and motion control, while gearboxes provide speed adjustment and torque conversion. In this blog post, we will explore the significance of gears and gearboxes in turret systems.
1. Rotation and Traverse: Gears and gearboxes are essential for the rotation and traverse of turrets. Turrets require the ability to rotate horizontally or vertically to track targets and engage them accurately. Gears transmit power from the motors or actuators to the turret platform, enabling controlled and precise rotation. Gearboxes offer speed control and torque conversion, allowing operators to adjust the rotational speed and traverse motion to suit different engagement scenarios.
2. Weapon Elevation and Depression: Turret systems often include weapon systems that require precise elevation and depression control. Gears and gearboxes enable the adjustment of the weapon’s vertical movement, allowing it to be elevated or depressed to acquire and engage targets at varying distances. Gearboxes offer the necessary torque conversion and speed control, ensuring smooth and accurate elevation and depression of the weapon.
3. Weapon Stabilization: Gears and gearboxes are also employed in turret systems to provide weapon stabilization capabilities. Stabilization systems counteract the motion and vibrations of the platform, maintaining the weapon’s stability and accuracy during turret movement or vehicle motion. Gears and gearboxes play a vital role in transmitting the stabilization signals and controlling the movement of stabilizing mechanisms, contributing to improved accuracy and target engagement.
4. Speed Control and Tracking: Gears and gearboxes facilitate speed control and tracking in turret systems. They enable the tracking of moving targets by allowing the turret to rotate at the required speed to keep pace with the target’s movement. Gearboxes offer speed adjustment capabilities, allowing operators to control the rotation speed and track targets effectively. This ensures precise tracking and engagement, especially in dynamic combat situations.
5. Durability and Reliability: Turret systems operate in demanding environments, including combat scenarios and extreme weather conditions. Gears and gearboxes used in turret systems are designed to withstand these rigorous conditions. They are constructed with durable materials and precision engineering to ensure reliability and longevity. Proper lubrication and maintenance of gears and gearboxes are crucial to minimize wear and tear, ensuring optimal performance and maximizing the lifespan of turret systems.
Gears and gearboxes are vital components in turret systems, enabling precise rotation, elevation, stabilization, and tracking capabilities. Their presence ensures the effectiveness, accuracy, and reliability of turret systems in various applications. As technology advances, gears and gearboxes will continue to play a crucial role in enhancing the performance and versatility of turret systems, contributing to the capabilities and success of defense operations.
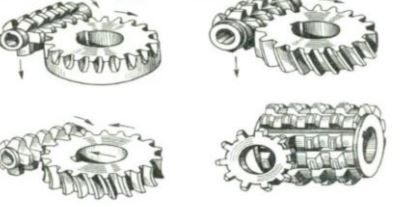
Gear Manufacturing Processes: From Design to Production
Gears are essential components used in various industries, from automotive and aerospace to machinery and robotics. The manufacturing of gears requires a precise and systematic approach to ensure optimal performance, durability, and reliability. In this blog post, we will explore the key steps involved in gear manufacturing processes, from design to production.
Gear Design:
The first step in gear manufacturing is the design phase. Gear designers utilize specialized software and tools to create the gear geometry, taking into account factors such as tooth profile, module, pressure angle, and pitch diameter. The design process also involves considering the specific application requirements, load capacity, and desired performance characteristics of the gear.
Material Selection:
Choosing the right material for gear production is crucial to ensure strength, wear resistance, and durability. Commonly used materials for gears include alloy steels, stainless steels, and non-ferrous metals like bronze and brass. The material selection is based on factors such as load capacity, operating conditions, and cost considerations.
Gear Cutting:
Gear cutting is a critical process in gear manufacturing. It involves removing material from a gear blank to create the desired tooth profile. There are several methods for gear cutting, including hobbing, shaping, milling, and broaching. Each method has its advantages and is chosen based on factors such as gear type, volume, and accuracy requirements.
Heat Treatment:
After gear cutting, the gears often undergo heat treatment processes to enhance their mechanical properties. Heat treatment techniques such as carburizing, quenching, and tempering are employed to achieve desired hardness, toughness, and wear resistance. Heat treatment ensures that the gears can withstand the stresses and loads they will encounter during operation.
Finishing Operations:
Once the gears have undergone heat treatment, they go through various finishing operations. These include grinding, honing, lapping, and deburring to achieve the desired surface finish, dimensional accuracy, and tooth profile quality. Finishing operations are essential for reducing noise, improving gear meshing, and ensuring smooth and efficient operation.
Inspection and Quality Control:
Throughout the manufacturing process, gears undergo rigorous inspection and quality control measures. This involves using precision measurement tools and equipment to check dimensional accuracy, tooth profile, surface finish, and hardness. Advanced inspection techniques such as coordinate measuring machines (CMMs) and non-destructive testing methods are employed to ensure the gears meet the required specifications and standards.
Assembly and Testing:
In some applications, gears are assembled into gearboxes or transmission systems. This involves carefully aligning the gears, shafts, and bearings to ensure proper gear meshing and smooth operation. Gear assemblies are then subjected to functional testing, including load testing, noise testing, and endurance testing, to verify their performance under real-world conditions.
Gear manufacturing is a complex and precise process that involves multiple steps, from gear design to production. Each step, from gear cutting and heat treatment to finishing operations and quality control, is crucial in ensuring the final gears meet the required specifications and performance standards. By following a systematic approach and employing advanced manufacturing techniques, gear manufacturers can produce high-quality gears that provide reliable and efficient performance in various applications.
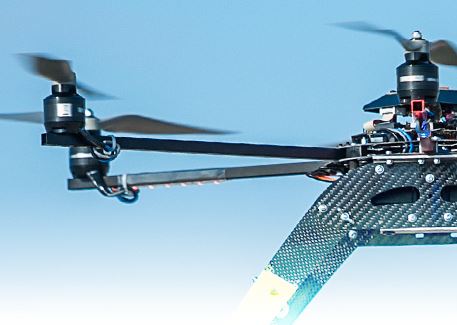
The Role of Gears in Unmanned Aerial Vehicles (UAVs)
Unmanned Aerial Vehicles (UAVs), commonly known as drones, have revolutionized various industries, including aerial photography, delivery services, surveillance, and agriculture. Within these UAVs, gears play a critical role in enabling efficient and precise flight control. Gears facilitate power transmission and motion control, ensuring smooth and reliable operation. In this blog post, we will explore the significance of gears in unmanned aerial vehicles.
1. Flight Control: Gears are essential components in the flight control systems of UAVs. They enable the transmission of power from the motors to the propellers, which generate the necessary thrust for flight. Gears ensure that the rotational motion produced by the motors is efficiently transferred to the propellers, resulting in precise control over the UAV’s movement, including ascent, descent, and directional changes.
2. Speed Control: Controlling speed is crucial in UAVs to achieve stable flight and maneuverability. Gears offer speed control capabilities by providing different gear ratios. By changing gears, UAV operators can adjust the rotational speed of the propellers, allowing for varying flight speeds based on specific requirements. Speed control through gears enables UAVs to optimize their performance for different tasks, such as aerial photography, search and rescue, or surveillance.
3. Torque Conversion: UAVs often require torque conversion to adapt to changing flight conditions or payload requirements. Gears facilitate torque conversion by adjusting the rotational force transmitted to the propellers. This allows UAVs to generate the necessary thrust to overcome external forces, such as wind resistance, or to carry heavier payloads. Proper torque conversion ensures efficient flight performance and stability in diverse operating conditions.
4. Durability and Efficiency: Gears used in UAVs are designed to be lightweight yet durable to maximize flight efficiency and endurance. They are constructed using high-quality materials, such as aluminum alloys or composites, to ensure strength and reliability while minimizing weight. The use of durable gears contributes to the overall longevity and operational efficiency of UAVs, enabling longer flight times and reducing maintenance requirements.
5. Noise Reduction: In addition to their functional role, gears also impact the acoustic performance of UAVs. Noise reduction is a critical consideration, especially in applications such as aerial photography or surveillance, where minimizing noise interference is essential. Carefully designed and properly lubricated gears can help reduce noise levels generated by the propulsion system, resulting in quieter operation and improved overall performance.
Gears are integral components in unmanned aerial vehicles (UAVs), enabling flight control, speed adjustment, torque conversion, durability, and noise reduction. Their presence ensures precise and efficient operation, allowing UAVs to perform various tasks with stability and reliability. As UAV technology continues to advance, gears will continue to play a vital role in enhancing flight performance, autonomy, and versatility, driving the future of unmanned aerial vehicles toward new possibilities in different industries.
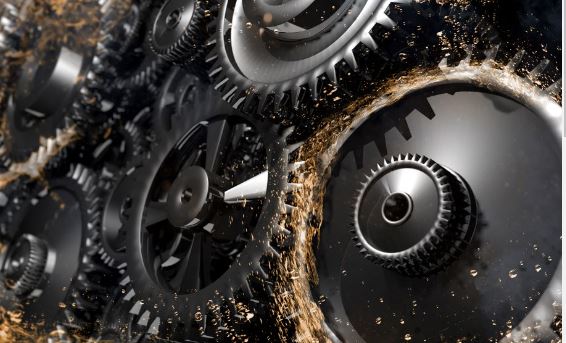
Couplings and Backstops Manufacturing Processes: Ensuring Efficient Power Transmission
Couplings and backstops are essential components used in various industries for efficient power transmission and motion control. They play a crucial role in connecting rotating shafts, absorbing misalignment, and preventing reverse rotation. The manufacturing of couplings and backstops involves precise processes to ensure durability, reliability, and optimal performance. In this blog post, we will explore the key steps involved in couplings and backstops manufacturing processes.
1. Design and Engineering: The manufacturing process begins with the design and engineering phase. Coupling and backstop designers utilize CAD software and advanced engineering principles to create detailed designs. The design process involves considering factors such as torque capacity, misalignment compensation, operating conditions, and specific industry requirements.
2. Material Selection: Choosing the right materials for couplings and backstops is crucial to ensure strength, durability, and performance. Common materials used for manufacturing include alloy steels, stainless steels, and various engineering plastics. The material selection is based on factors such as torque capacity, operating conditions (including temperature and corrosive environments), and cost considerations.
3. Machining and Fabrication: Once the design is finalized, the manufacturing process begins with machining and fabrication. This involves shaping and forming the coupling or backstop components through processes such as milling, turning, drilling, and grinding. CNC machines are often used to ensure precision and consistency in the manufacturing process.
4. Heat Treatment and Surface Treatment: Couplings and backstops often undergo heat treatment processes to enhance their mechanical properties. Heat treatment techniques such as quenching and tempering are employed to achieve the desired hardness, toughness, and wear resistance. Surface treatment methods such as coating or plating may also be applied to provide additional protection against corrosion and wear.
5. Assembly and Balancing: Once the individual components are manufactured and treated, they are assembled to create the complete coupling or backstop mechanism. Assembly involves precise fitting and alignment of the components to ensure smooth operation and optimal performance. Balancing is also performed to minimize vibration and ensure stable operation at high rotational speeds.
6. Testing and Quality Control: Couplings and backstops undergo rigorous testing and quality control measures to ensure their performance and reliability. Functional tests, including torque testing, misalignment testing, and endurance testing, are conducted to verify the components’ ability to handle specified loads and operating conditions. Quality control inspections, including dimensional checks and surface finish evaluations, are performed to ensure adherence to design specifications and standards.
7. Packaging and Delivery: After testing and quality control, the couplings and backstops are properly packaged to ensure protection during transportation and storage. Packaging materials and methods are chosen to safeguard the components and prevent any damage during handling and shipping. The products are then delivered to the customers or integrated into larger systems or machinery.
The manufacturing of couplings and backstops involves a series of precise processes to ensure durability, reliability, and efficient power transmission. From design and material selection to machining, heat treatment, assembly, and quality control, each step plays a vital role in producing high-quality components. By following stringent manufacturing processes and adhering to quality control measures, manufacturers can deliver couplings and backstops that meet the performance requirements and specifications of various industries.
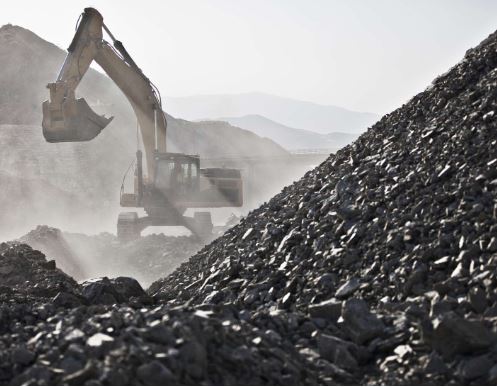
The Significance of Gears and Gearboxes in the Mining Industry
The mining industry plays a vital role in extracting valuable minerals and resources from the earth. Within this industry, gears and gearboxes are critical components used in mining machinery and equipment to enable efficient and powerful operations. Gears facilitate power transmission and motion control, while gearboxes provide speed adjustment and torque conversion. In this blog post, we will explore the importance of gears and gearboxes in the mining industry.
1. Power Transmission in Heavy Equipment: Mining operations require a wide range of heavy machinery, such as excavators, haul trucks, and crushers, to extract and transport minerals. Gears and gearboxes are integral in transmitting power from the engines to the various components of these machines. They ensure that the rotational motion produced by the engine is efficiently transferred to drive the movement and operation of the equipment, providing the necessary power for mining tasks.
2. Speed Control and Torque Conversion: Gears and gearboxes offer speed control and torque conversion capabilities in mining machinery. Different mining processes require varying speeds and torque levels to meet specific requirements. Gears and gearboxes allow operators to adjust the gear ratios to achieve the desired speed and torque output, enabling precise control over the equipment’s performance. This flexibility enhances the efficiency and effectiveness of mining operations, optimizing productivity and resource utilization.
3. Conveyor Systems: Conveyor systems are commonly used in mining operations to transport bulk materials over long distances. Gears and gearboxes play a crucial role in these systems, driving the movement of conveyor belts and facilitating efficient material handling. Gearboxes provide the necessary torque conversion and speed control to ensure the smooth and continuous operation of the conveyor system, enabling the seamless transfer of mined materials.
4. Hoisting and Lifting Equipment: Mining often involves the hoisting and lifting of heavy loads, such as ore, equipment, and personnel. Gears and gearboxes are essential components in hoisting and lifting equipment, including mine shaft hoists and cranes. They enable the precise control of lifting operations, ensuring safe and efficient movement of heavy loads in mining shafts or on the surface. Gearboxes offer the ability to adjust the lifting speed and control the load with accuracy and safety.
5. Durability and Reliability: Mining operations are characterized by harsh and demanding environments, including abrasive materials, dust, high loads, and extreme temperatures. Gears and gearboxes used in mining machinery are designed to withstand these challenging conditions. They are built with robust materials and precision engineering to ensure durability and reliability. Proper maintenance and lubrication of gears and gearboxes are crucial for their longevity, minimizing downtime and maximizing the productivity of mining operations.
Gears and gearboxes play a crucial role in the mining industry, enabling power transmission, speed control, and torque conversion in various mining machinery and equipment. From heavy equipment power transmission to the efficient operation of conveyor systems and hoisting equipment, gears and gearboxes contribute to the efficiency, productivity, and safety of mining operations. As the mining industry continues to evolve, advancements in gear and gearbox technology will further enhance productivity, sustainability, and worker safety, driving the future of mining towards more efficient and responsible practices.