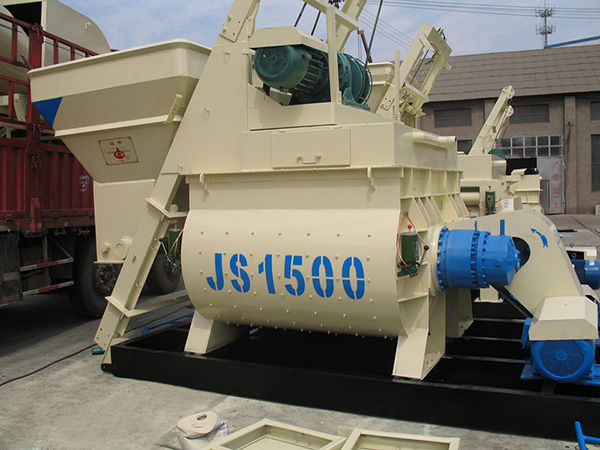
The Essential Role of Twinshaft Reducers in Concrete Mixers
Twinshaft reducers are crucial components in the operation of concrete mixers. These devices control and adjust the rotational speed of the mixer’s shafts, ensuring a consistent and compelling mix. In a concrete mixer, the twin-shaft reducer manages the torque and speed required to mix the concrete components uniformly. This is particularly important in large-scale or industrial concrete operations where consistency and efficiency are key.
Ermaksan Gear, recognized for its expertise in industrial gear systems, likely applies advanced design and manufacturing techniques to produce twin-shaft reducers that are both robust and reliable. The focus on precision engineering ensures that their twin-shaft reducers can handle the heavy loads and high demands typical in concrete mixing operations, translating to better performance and longevity of the mixers.
Enhancing Durability and Performance in Harsh Conditions
Concrete mixers operate in demanding environments, often dealing with heavy materials and continuous operation. Twinshaft reducers in these mixers must be exceptionally durable to withstand these conditions. Therefore, companies like Ermaksan Gear would focus on using high-quality materials and state-of-the-art manufacturing processes to ensure the reducers’ resilience and durability. This includes resistance to wear and tear, the ability to operate efficiently under various loads, and minimal need for maintenance.
In addition to durability, the performance of twin-shaft reducers is critical. Ermaksan Gear’s reducers are likely designed to provide optimal torque and rotational speed, which are essential for adequate concrete mixing. The precise control of these factors results in a more uniform and consistent concrete mix, which is crucial for the quality of the final product.
The Impact of Twinshaft Reducer Technology in Construction
Innovations Leading to Increased Productivity
Technological advancements in the design and manufacturing of twin-shaft reducers, such as those produced by Ermaksan Gear, directly impact the efficiency and productivity of concrete mixers. Innovations in gear technology, material science, and engineering design contribute to more efficient reducers, requiring less energy and time to achieve the desired mixing results. This increased efficiency is cost-effective and enhances the overall throughput of concrete production.
Furthermore, advanced twin-shaft reducers can contribute to the mixer’s ability to handle different types of concrete mixes – from standard to high-performance concrete – with ease. This versatility is a significant advantage in the construction industry, where other projects may require different types of concrete.
Supporting Sustainable and Safe Construction Practices
Modern twin-shaft reducers are also designed with sustainability and safety in mind. Energy-efficient designs contribute to lower energy consumption, reducing the environmental footprint of construction projects. Additionally, the reliability and durability of these components reduce the frequency of repairs and replacements, contributing to more sustainable construction practices.
Safety is another critical aspect. Advanced reducers are designed to operate smoothly and predictably, reducing the risk of mechanical failures that could lead to safety hazards on the construction site. This reliability is crucial, considering construction projects’ often high-stakes and time-sensitive nature.
Twinshaft Reducers in Concrete Mixers: Optimizing Mixing and Quality
Precision and Quality Control in Concrete Production
The precision of twin-shaft reducers in concrete mixers is critical to their utility. These reducers enable precise control over the mixing process, which is essential for achieving the desired quality of concrete. In scenarios where the consistency and composition of the concrete are paramount, such as in high-precision construction projects, the role of a twin-shaft reducer becomes even more significant. Ermaksan Gear’s reducers likely incorporate advanced design features that allow for fine-tuning the mixing process, resulting in a high-quality concrete mix.
Quality control in concrete production is not just about the final product but also about the production process’s efficiency and reliability. Reducers designed by companies like Ermaksan Gear help ensure that the mixers operate consistently at optimal parameters, minimizing the chances of errors or inconsistencies in the concrete mix. This level of control is crucial for maintaining the standards required in modern construction projects.
Adapting to Evolving Construction Needs with Advanced Reducers
The construction industry constantly evolves, with new materials, techniques, and standards emerging regularly. Twinshaft reducers must adapt to these changes, especially those designed and manufactured by companies like Ermaksan Gear. This could involve incorporating new materials that offer better performance or resilience or redesigning the reducers to be more energy-efficient and environmentally friendly.
Ermaksan Gear’s approach to designing and producing twin-shaft reducers likely involves a commitment to continuous improvement and innovation. By staying abreast of the latest trends and advancements in the construction industry, they can ensure that their reducers meet the ever-changing needs of their clients. This adaptability is essential for maintaining a competitive edge in the industry and contributing to the advancement of construction technology.
Future Trends and Developments in Twinshaft Reducer Technology
Emerging Technologies and Their Impact on Reducer Design
Emerging engineering and materials science trends will likely influence the future of twin-shaft reducer technology. Advancements in nanotechnology, composite materials, and smart manufacturing processes could lead to the development of more efficient, durable, and intelligent reducers. For a company like Ermaksan Gear, staying ahead and incorporating these trends into their products will be critical to their continued success and relevance in the market.
Smart technology, in particular, could revolutionize the way twin-shaft reducers are used in concrete mixers. Integrating sensors and IoT (Internet of Things) connectivity could allow for real-time monitoring and adjustments of the reducers, further optimizing the mixing process and enhancing the quality of the concrete. This level of technological integration could also lead to predictive maintenance capabilities, reducing downtime and increasing the overall efficiency of the mixers.
Sustainability and Environmental Considerations in Reducer Design
As the world increasingly focuses on sustainability and environmental responsibility, these factors are becoming more important in industrial design, including twin-shaft reducers. Future designs of these components will likely emphasize reducing energy consumption and using environmentally friendly materials. This shift is crucial for complying with regulations and standards and meeting the growing demand for sustainable construction practices.
Ermaksan Gear, in alignment with these trends, might focus on developing reducers that are both efficient and have a reduced environmental impact. This could involve using recycled materials, improving the efficiency of the gear systems to reduce energy consumption, or designing the reducers for easier recycling at the end of their lifespan. Such considerations will benefit the environment and align with the broader goals of the construction industry to become more sustainable and responsible.
Twinshaft reducers play an indispensable role in the efficiency and effectiveness of concrete mixers, a fact that companies like Ermaksan Gear are well aware of. Their precision engineering, durability, and adaptability make them vital for ensuring consistent quality in concrete production, and meeting the evolving demands of the construction industry.
As we look to the future, the potential integration of emerging technologies and a growing emphasis on sustainability are set further to enhance the capabilities and impact of these essential components. Ermaksan Gear’s commitment to innovation and quality positions them as key players in advancing the technology behind twin-shaft reducers, contributing significantly to the global advancement and sustainability of construction practices.
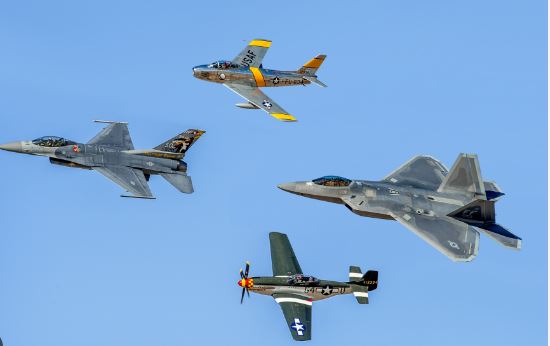
The Role of Gears and Gearboxes in Helicopters, Aircraft, and Armored Vehicles
Helicopters, aircraft, and armored vehicles are essential components of modern aviation and military operations. Within these vehicles, gears and gearboxes play a crucial role in power transmission, control, and maneuverability. Gears enable power transmission and motion control, while gearboxes provide speed adjustment and torque conversion. In this blog post, we will explore the significance of gears and gearboxes in helicopters, aircraft, and armored vehicles.
1. Helicopters: Gears and gearboxes are integral to the operation of helicopters, enabling precise control and maneuverability. They facilitate power transmission from the engine to the main and tail rotors, allowing for controlled lift, propulsion, and directional changes. Gears transmit power to the rotors, while gearboxes offer speed adjustment and torque conversion, ensuring optimal rotor speed for various flight regimes, such as hover, forward flight, or vertical takeoff and landing (VTOL).
2. Aircraft: Gears and gearboxes are also used in various aircraft systems to facilitate power transmission and control. They play a crucial role in systems such as landing gear retraction and extension, flap deployment, and engine accessory drives. Gears transmit power to different components, while gearboxes provide speed adjustment and torque conversion, optimizing the performance of these systems during takeoff, landing, and cruising phases of flight.
3. Armored Vehicles: In armored vehicles, gears and gearboxes contribute to power transmission, control, and mobility. They facilitate the transfer of power from the engine to the wheels or tracks, enabling propulsion and maneuverability. Gears ensure the efficient transmission of torque, while gearboxes offer speed adjustment and torque conversion, allowing operators to control the vehicle’s speed and optimize performance for various terrain conditions.
4. Maneuvering and Steering: Gears and gearboxes are crucial for maneuvering and steering in helicopters, aircraft, and armored vehicles. In helicopters, they enable cyclic and collective control, allowing for precise control of rotor blades and flight control surfaces. In aircraft, they facilitate aileron, elevator, and rudder control, enabling roll, pitch, and yaw movements. In armored vehicles, gears and gearboxes provide steering control, allowing for precise maneuvering and directional changes.
5. Durability and Reliability: Gears and gearboxes used in helicopters, aircraft, and armored vehicles are designed to withstand demanding operating conditions. They are built with durable materials and precise engineering to ensure reliability and longevity. Proper lubrication and maintenance of gears and gearboxes are crucial to minimize wear and tear, ensuring optimal performance and maximizing the lifespan of these vehicles.
Gears and gearboxes are vital components in helicopters, aircraft, and armored vehicles, enabling power transmission, control, and maneuverability. From rotor systems and flight control surfaces to propulsion systems and vehicle mobility, gears and gearboxes play a crucial role in ensuring efficient and reliable operation. As technology advances, gears and gearboxes will continue to evolve, enhancing the performance and capabilities of helicopters, aircraft, and armored vehicles, and contributing to the success of aviation and military operations.
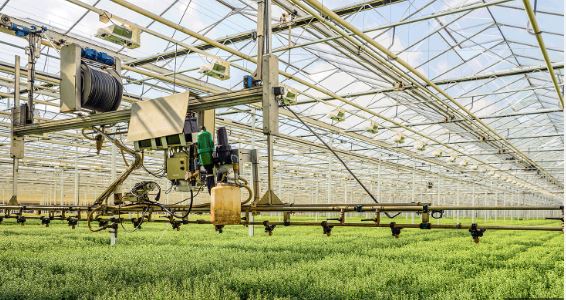
The Role of Gears and Gearboxes in Livestock Equipment and Greenhouse Automation
Livestock equipment and greenhouse automation systems play a crucial role in modern agriculture. Within these applications, gears and gearboxes are essential components that enable precise control, motion transmission, and automation. Gears facilitate power transmission and motion control, while gearboxes provide speed adjustment and torque conversion. In this blog post, we will explore the significance of gears and gearboxes in livestock equipment and greenhouse automation.
1. Livestock Equipment: a. Feed Mixers: Feed mixers are used to blend and distribute animal feed. Gears and gearboxes are employed in these machines to facilitate the mixing and distribution processes. They ensure the efficient rotation and movement of mixing blades or augers, allowing for thorough and consistent mixing of feed ingredients. b. Milking Machines: Milking machines used in dairy operations rely on gears and gearboxes for the operation of vacuum pumps and pulsators. These components facilitate the controlled suction and release of milk from he udders, ensuring efficient and hygienic milking processes.
2. Greenhouse Automation: a. Curtain Systems: Greenhouses often utilize curtain systems for environmental control. Gears and gearboxes are utilized to open and close these curtains, allowing for proper ventilation and temperature regulation. Gearboxes enable precise control over the curtain movement, ensuring optimal growing conditions for plants. b. Ventilation Systems: Gears and gearboxes play a role in automating greenhouse ventilation systems. They control the opening and closing of vents or louvers, enabling the regulation of airflow and temperature inside the greenhouse. Gearboxes offer speed adjustment, allowing for fine-tuning of ventilation rates based on environmental conditions.
3. Poultry Equipment: a. Egg Collection Systems: In poultry farms, automated egg collection systems rely on gears and gearboxes. They facilitate the movement of conveyor belts or trays, guiding eggs from the nests to collection points. Gears and gearboxes ensure smooth and reliable transportation of eggs, optimizing efficiency in egg production. b. Poultry Feeding Systems: Poultry feeding systems often utilize gear and gearbox mechanisms to regulate the distribution of feed. They control the movement of feed dispensers, ensuring accurate and timely delivery of feed to poultry. Gearboxes offer speed adjustment, allowing for precise control over feed distribution rates.
4. Durability and Reliability: Gears and gearboxes used in livestock equipment and greenhouse automation are designed to withstand challenging operating conditions. They are constructed with durable materials and precise engineering to ensure reliability and longevity. Regular maintenance and lubrication of gears and gearboxes are crucial to minimize wear and tear, ensuring optimal performance and maximizing the lifespan of these systems.
Gears and gearboxes play a vital role in livestock equipment and greenhouse automation, enabling precise control, motion transmission, and automation. Whether it’s feed mixers, milking machines, greenhouse curtain systems, or poultry equipment, these components contribute to the efficiency, productivity, and automation of agricultural processes. As technology continues to advance, gears and gearboxes will continue to evolve, further enhancing the capabilities and performance of livestock equipment and greenhouse automation systems, driving the agriculture industry towards increased efficiency and sustainability.

The Role of Gears and Gearboxes in Missile Systems
Missile systems are critical components of modern defense capabilities, providing the ability to engage targets accurately and rapidly. Within these systems, gears and gearboxes play a crucial role in enabling the precise control and movement of various missile components. Gears facilitate power transmission and motion control, while gearboxes provide speed adjustment and torque conversion. In this blog post, we will explore the significance of gears and gearboxes in missile systems.
1. Missile Guidance and Control: Gears and gearboxes are integral to the guidance and control systems of missiles. They facilitate the precise movement and adjustment of control surfaces, such as fins or vanes, which help steer the missile during flight. Gears transmit power from actuators to these control surfaces, allowing for accurate and responsive control of the missile’s trajectory. Gearboxes enable speed control and torque conversion, ensuring precise movement and adjustment of the control surfaces.
2. Thrust Vector Control: Missiles with thrust vector control (TVC) capability utilize gears and gearboxes to redirect the engine’s exhaust for maneuvering. Gears transmit power from the actuators to the nozzle or vanes, enabling precise control over the direction of the exhaust flow. Gearboxes provide the necessary speed adjustment and torque conversion to optimize thrust vector control, allowing for agile maneuverability and target tracking during flight.
3. Firing Mechanisms: Gears and gearboxes are employed in the firing mechanisms of missile systems. They enable the precise and controlled release of the missile from its launch platform or container. Gears transmit power from the initiation system to the locking mechanisms or release mechanisms, ensuring smooth and reliable missile deployment. Gearboxes offer speed control, ensuring the release mechanism operates at the appropriate speed for safe and accurate missile launch.
4. Payload Deployment: Missiles often carry various types of payloads, such as warheads, decoys, or sensors. Gears and gearboxes play a role in the deployment of these payloads. They facilitate the controlled release or separation of the payload from the missile body, ensuring proper timing and positioning. Gearboxes offer speed adjustment and torque conversion, allowing for precise deployment of payloads, such as the separation of warheads or the ejection of decoys.
5. Durability and Reliability: Missile systems operate under extreme conditions, including high speeds, rapid accelerations, and intense vibrations. Gears and gearboxes used in missile systems are designed to withstand these rigorous environments. They are constructed with durable materials and precision engineering to ensure reliability and longevity. Proper lubrication and maintenance of gears and gearboxes are crucial to minimize wear and tear, ensuring optimal performance and the successful operation of missile systems.
Gears and gearboxes play a vital role in missile systems, enabling precise control, thrust vectoring, firing mechanisms, and payload deployment. Their presence ensures the effectiveness, accuracy, and reliability of missile systems in various defense applications. As technology advances, gears and gearboxes will continue to play a crucial role in enhancing the performance and capabilities of missile systems, contributing to the defense capabilities and success of modern military operations.
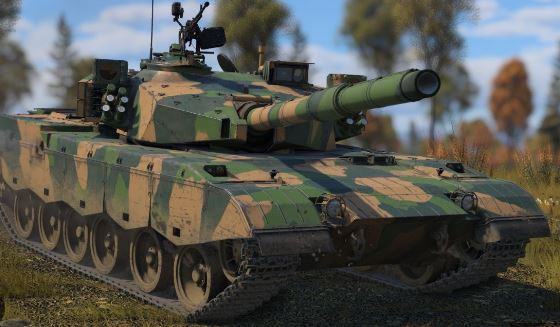
The Role of Gears and Gearboxes in Tanks
Tanks are powerful military vehicles designed for combat on the battlefield. Within these armored machines, gears and gearboxes are critical components that enable mobility, power transmission, and precise control. Gears facilitate the transfer of power from the engine to the tracks, while gearboxes provide speed adjustment and torque conversion. In this blog post, we will explore the significance of gears and gearboxes in tanks.
1. Track Propulsion: Gears and gearboxes play a crucial role in the propulsion system of tanks. Gears facilitate power transmission from the engine to the drive sprockets, which engage with the tracks, propelling the tank forward or backward. Gearboxes provide speed adjustment, allowing operators to control the rotational speed of the tracks. This enables tanks to traverse various terrains with efficiency and precision.
2. Steering and Maneuverability: Gears and gearboxes contribute to the steering and maneuvering capabilities of tanks. Tanks often employ differential steering, where the tracks on each side can move independently. Gears enable differential power distribution, allowing tanks to make precise turns and navigate challenging terrain. Gearboxes provide the necessary control over the rotational speed and torque applied to each track, ensuring smooth and responsive maneuverability.
3. Speed Control: Effective speed control is essential in tank operations. Gears and gearboxes offer speed control capabilities by providing different gear ratios. Tank operators can adjust the gear ratio to achieve the desired speed, whether it’s for rapid movement during offensive operations or slow and controlled movement for defensive or reconnaissance purposes. Gearboxes allow for precise speed adjustment, ensuring tanks can operate efficiently at different speeds.
4. Torque Conversion: Tanks require significant torque to overcome obstacles and operate in challenging terrain. Gears and gearboxes facilitate torque conversion by adjusting the rotational force transmitted to the tracks. They enable tanks to generate the necessary torque to climb steep slopes, traverse rough terrains, or push through obstacles. Efficient torque conversion enhances the mobility and operational capabilities of tanks in various combat scenarios.
5. Durability and Reliability: Tanks operate in harsh and demanding environments, subject to extreme temperatures, vibrations, and combat conditions. Gears and gearboxes used in tanks are designed to withstand these rigorous conditions. They are constructed with durable materials and precision engineering to ensure reliability and longevity. Regular maintenance and lubrication of gears and gearboxes are crucial to minimize wear and tear, ensuring optimal performance and maximizing the lifespan of tanks.
Gears and gearboxes are integral components in tanks, enabling track propulsion, steering, speed control, torque conversion, durability, and reliability. Their presence ensures the mobility, maneuverability, and operational effectiveness of tanks on the battlefield. As military technology continues to advance, gears and gearboxes will play a crucial role in enhancing the capabilities and performance of tanks, contributing to the armored forces’ effectiveness and success in modern warfare.
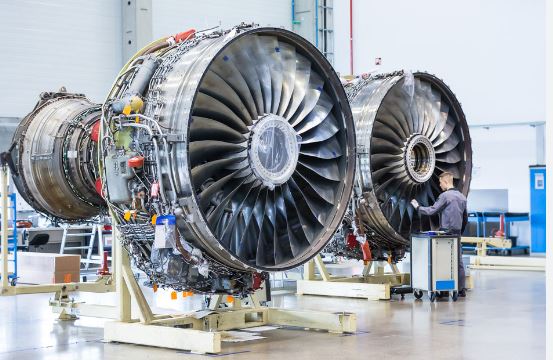
The Role of Gears and Gearboxes in the Aviation Industry
The aviation industry is known for its constant pursuit of innovation and advanced engineering solutions. Aircraft are equipped with numerous complex systems and components to enable safe and efficient travel through the air. One such crucial component is gears and gearboxes. Gears play a vital role in the aviation industry and have a significant impact on the performance, safety, and durability of aircraft. In this blog post, we will explore why gears and gearboxes are important in the aviation industry.
1. Power Transmission: Aircraft require effective transmission of power to propel and control their movement. Gears and gearboxes are integral in this power transmission process. They play a key role in transmitting power from the engines to various systems, such as the propellers or jet engines. Gears allow the engines to transfer rotational motion to generate thrust, enabling the aircraft to accelerate, climb, and maneuver. Gearboxes help in controlling the speed and torque of the engines, ensuring optimal performance and fuel efficiency.
2. Reduction of Rotational Speed: In aviation, engines typically operate at very high rotational speeds, while other aircraft systems require lower speeds for optimal functioning. Gears and gearboxes are used to reduce the rotational speed of the engines and transmit it to different components, such as generators, hydraulic pumps, or flight control systems. By reducing the rotational speed, gears and gearboxes enable these systems to operate efficiently and safely within their designed parameters.
3. Mechanical Advantage and Force Multiplication: Gears are renowned for their ability to provide mechanical advantage and force multiplication. In the aviation industry, this is particularly important for flight control systems. By utilizing gears and gearboxes, the pilot’s input can be translated into precise and amplified movement of control surfaces such as ailerons, elevators, and rudders. This allows for responsive and accurate control of the aircraft during various flight phases, including takeoff, landing, and maneuvering.
4. Load Distribution and Durability: Aircraft engines generate immense power and torque, which can place significant stress on various components. Gears and gearboxes aid in distributing the load and reducing stress on critical parts, improving overall durability and longevity. They help balance the forces acting on the engines and enable the aircraft to withstand high-stress conditions, such as during rapid acceleration or sudden changes in flight trajectory.
5. Backup and Redundancy: Reliability and redundancy are paramount in aviation to ensure the safety of passengers and crew. Gears and gearboxes play a crucial role in providing backup systems. In the event of a failure in the primary gear system, redundant gear sets or gearboxes can be engaged to maintain the functionality of essential systems. This redundancy ensures that even in the face of mechanical issues, the aircraft can continue to operate safely until maintenance or repairs can be performed.
Gears and gearboxes are indispensable components in the aviation industry. From power transmission and force multiplication to load distribution and redundancy, they play a vital role in ensuring safe and efficient aircraft operations. The continuous advancements in gear technology contribute to the overall improvement in aircraft performance, reliability, and passenger safety in the dynamic world of aviation.

The Role of Gears and Gearboxes in the Construction Industry
The construction industry is a dynamic sector that involves the creation of infrastructure and buildings. Within this industry, gears and gearboxes play a crucial role in various construction machinery and equipment, facilitating efficient and powerful operation. Gears enable power transmission and motion control, while gearboxes provide speed adjustment and torque conversion. In this blog post, we will explore the significance of gears and gearboxes in the construction industry.
1. Heavy Equipment Power Transmission: Construction sites require a wide range of heavy machinery, such as excavators, cranes, and bulldozers, to perform tasks like digging, lifting, and moving heavy materials. Gears and gearboxes are essential in transmitting power from the engines to the various components of these machines. They ensure that the rotational motion produced by the engine is effectively transferred to drive the movement of the equipment, providing the necessary power for construction operations.
2. Speed Control and Torque Conversion: Gears and gearboxes offer speed control and torque conversion capabilities in construction machinery. Different construction tasks require varying speeds and torque levels to meet specific requirements. Gears and gearboxes allow operators to adjust the gear ratio to achieve the desired speed and torque output, enabling precise control over the equipment’s performance. This versatility enhances the efficiency and effectiveness of construction operations, ensuring optimal productivity.
3. Cranes and Lifting Equipment: Cranes and lifting equipment are indispensable in the construction industry for lifting and moving heavy loads. Gears and gearboxes are critical components in these machines, providing the necessary power transmission and control for the lifting mechanisms. They ensure smooth and precise lifting operations, allowing for safe and efficient movement of materials and equipment at construction sites. Gearboxes enable operators to adjust the lifting speed and control the load with accuracy and precision.
4. Concrete Mixers and Pumps: Concrete mixers and pumps are commonly used in construction projects for preparing and delivering concrete to the desired locations. Gears and gearboxes are essential in these machines to facilitate the mixing and pumping processes. They ensure the proper rotation and movement of the mixing drum and pump components, enabling the consistent and efficient delivery of concrete to the construction site. Gearboxes offer the ability to adjust the speed and torque to match the specific requirements of the task.
5. Durability and Reliability: Construction sites often present challenging and demanding conditions, including heavy loads, vibrations, and rough terrains. Gears and gearboxes used in construction machinery are designed to withstand these rigorous environments. They are built with sturdy materials and precision engineering to ensure durability and reliability. Proper maintenance and lubrication of gears and gearboxes contribute to their longevity, minimizing downtime and maximizing the productivity of construction operations.
Gears and gearboxes play a vital role in the construction industry, enabling power transmission, speed control, and torque conversion in various construction machinery and equipment. From heavy equipment power transmission to the precise control of cranes and concrete mixers, gears and gearboxes are essential components that contribute to the efficiency and effectiveness of construction operations. As the construction industry continues to evolve, advancements in gear and gearbox technology will further enhance productivity, safety, and sustainability, driving the future of construction towards more innovative and efficient practices.

The Role of Gears and Gearboxes in the Food Industry
The food industry plays a crucial role in providing safe and nutritious food to consumers worldwide. Within this industry, gears and gearboxes are important components used in food processing and packaging equipment to ensure efficient and precise operations. Gears enable power transmission and motion control, while gearboxes provide speed adjustment and torque conversion. In this blog post, we will explore the significance of gears and gearboxes in the food industry.
1. Mixing and Blending: Mixing and blending are common processes in food production, whether it’s dough in bakeries or ingredients in large-scale food processing plants. Gears and gearboxes play a crucial role in mixers and blenders, ensuring the proper rotation and movement of mixing arms or blades. Gearboxes offer speed control and torque conversion, allowing operators to adjust mixing speeds and optimize the blending process for consistent product quality.
2. Conveyor Systems: Conveyor systems are widely used in the food industry to transport ingredients, finished products, or packaging materials throughout the production line. Gears and gearboxes are integral components in conveyor systems, driving the movement of conveyor belts and ensuring efficient material handling. Gearboxes offer the necessary torque conversion and speed control, allowing for smooth and continuous movement of food products along the production line.
3. Packaging and Filling Machines: Packaging and filling machines are essential in the food industry to package and seal various food products, such as beverages, snacks, or canned goods. Gears and gearboxes are critical components in these machines, facilitating the precise control of filling operations and ensuring accurate portioning of products. Gearboxes allow operators to adjust the rotational speed and torque, enabling the efficient packaging of food items with minimal waste or spillage.
4. Slicing and Cutting Equipment: Slicing and cutting equipment are used extensively in food processing, such as meat slicers, vegetable cutters, or bread slicers. Gears and gearboxes are vital in these machines, providing power transmission and motion control for the cutting blades. They ensure the smooth and precise movement of the blades, allowing for consistent and accurate slicing or cutting of food products. Gearboxes offer speed control, allowing operators to adjust cutting speeds based on the specific requirements of different food items.
5. Durability and Sanitation: In the food industry, equipment must meet strict hygiene standards and withstand frequent washdowns and sanitization processes. Gears and gearboxes used in food processing machinery are designed with materials and coatings that resist corrosion and maintain sanitary conditions. They are built to be durable and easy to clean, ensuring food safety and compliance with industry regulations.
Gears and gearboxes are essential components in the food industry, enabling power transmission, speed control, and precise motion in various food processing and packaging operations. From mixing and blending to conveyor systems and packaging machines, gears and gearboxes contribute to the efficiency, productivity, and quality of food production. As the food industry continues to evolve, advancements in gear and gearbox technology will further enhance efficiency, food safety, and the ability to meet the diverse demands of consumers around the world.
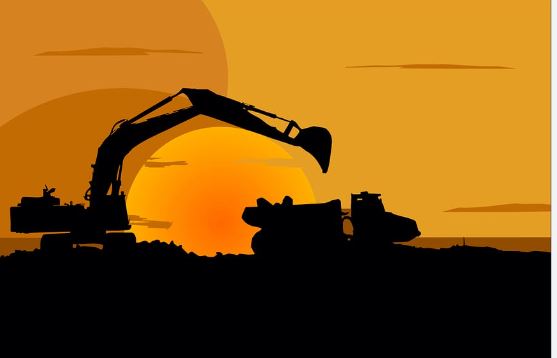
The Role of Gears and Gearboxes in the Heavy Equipment Industry
The heavy equipment industry plays a vital role in various sectors, including construction, mining, agriculture, and transportation. Within this industry, gears and gearboxes are crucial components used in heavy equipment to facilitate powerful and efficient operations. Gears enable power transmission and motion control, while gearboxes provide speed adjustment and torque conversion. In this blog post, we will explore the significance of gears and gearboxes in the heavy equipment industry.
1. Power Transmission: Gears and gearboxes are integral to power transmission in heavy equipment. From excavators and bulldozers to cranes and dump trucks, gears facilitate the transfer of power from the engine to various components, such as wheels, tracks, or lifting mechanisms. They ensure that the rotational motion produced by the engine is efficiently transferred to drive the movement and operation of the equipment, providing the necessary power for heavy-duty tasks.
2. Speed Control: Speed control is crucial in heavy equipment operations to match the requirements of different tasks and conditions. Gears and gearboxes offer the ability to adjust speed by providing different gear ratios. Operators can change gears to achieve the desired speed for specific operations, such as digging, lifting, or hauling. Gearboxes allow for speed adjustment and optimization, ensuring the equipment operates efficiently and safely in various working environments.
3. Torque Conversion: Heavy equipment often requires torque conversion to handle different loads and perform tasks effectively. Gears and gearboxes facilitate torque conversion by adjusting the rotational force transmitted to the equipment’s components. They enable the equipment to generate the necessary torque for tasks such as digging, lifting, or pushing heavy loads. The ability to convert torque efficiently enhances the performance and productivity of heavy equipment, allowing operators to handle demanding tasks with ease.
4. Load Handling and Material Movement: Heavy equipment is designed to handle substantial loads and move materials efficiently. Gears and gearboxes play a crucial role in this aspect by providing power transmission and control for lifting, hauling, or material handling operations. Whether it’s a crane lifting heavy objects or a loader moving materials, gears and gearboxes enable smooth and precise movement, ensuring efficient and safe handling of loads.
5. Durability and Reliability: Heavy equipment operates in demanding environments, exposed to extreme temperatures, rough terrains, and heavy loads. Gears and gearboxes used in heavy equipment are built to withstand these rigorous conditions. They are designed with durable materials and precision engineering to ensure durability and reliability. Proper maintenance and lubrication of gears and gearboxes are essential for their longevity, minimizing downtime and maximizing the productivity of heavy equipment operations.
Gears and gearboxes are essential components in the heavy equipment industry, enabling power transmission, speed control, and torque conversion in various equipment types. From excavators and loaders to cranes and dump trucks, gears and gearboxes contribute to the efficiency, productivity, and reliability of heavy equipment operations. As the heavy equipment industry continues to evolve, advancements in gear and gearbox technology will further enhance performance, safety, and sustainability, driving the future of heavy equipment towards more innovative and efficient practices.
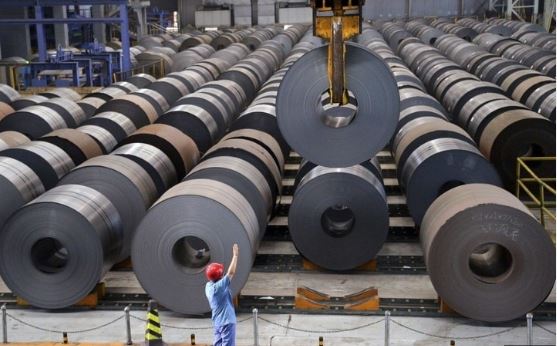
The Role of Gears and Gearboxes in the Iron and Steel Industry
The iron and steel industry plays a critical role in the production of essential materials for various sectors, including construction, automotive, and manufacturing. Within this industry, gears and gearboxes are vital components used in iron and steel manufacturing processes to ensure efficient and reliable operations. Gears facilitate power transmission and motion control, while gearboxes provide speed adjustment and torque conversion. In this blog post, we will explore the importance of gears and gearboxes in the iron and steel industry.
1. Rolling Mills: Rolling mills are essential in the iron and steel industry for the shaping and forming of metal products. Gears and gearboxes are crucial components in rolling mills, enabling the transmission of power to roll stands. They ensure the proper rotation and movement of rolls, which shape and reduce the thickness of metal sheets or billets. Gearboxes offer speed control and torque conversion, allowing operators to adjust rolling speeds and apply the required pressure for various metal-forming processes.
2. Continuous Casting: Continuous casting is a widely used method in the iron and steel industry to produce high-quality steel products. Gears and gearboxes are integral in continuous casting machines, which convert molten steel into solid billets or slabs. Gears facilitate the smooth movement of the casting molds, while gearboxes provide the necessary power transmission and speed control. Precise control over the casting process ensures consistent product quality and minimizes waste.
3. Cranes and Material Handling: Iron and steel manufacturing involves the movement and handling of heavy loads, such as molten metal, raw materials, and finished products. Gears and gearboxes play a crucial role in cranes and material handling equipment, providing power transmission and torque conversion for lifting, moving, and positioning heavy loads. They enable precise control and safe operation of cranes, ensuring efficient material handling throughout the iron and steel production process.
4. Steelmaking Processes: Steelmaking processes, such as blast furnaces and electric arc furnaces, require efficient power transmission and control for their operation. Gears and gearboxes are utilized in these processes to transmit power from motors or engines to various components, such as blowers, pumps, or electrode positioners. Gearboxes enable speed adjustment and torque conversion to optimize the performance of steelmaking equipment, ensuring efficient and reliable production.
5. Durability and Reliability: The iron and steel industry operates under demanding conditions, including high temperatures, heavy loads, and extreme pressures. Gears and gearboxes used in this industry are designed to withstand these rigorous environments. They are built with robust materials and precision engineering to ensure durability and reliability. Proper lubrication and maintenance of gears and gearboxes are essential for their longevity, minimizing downtime and maximizing the productivity of iron and steel manufacturing processes.
Gears and gearboxes are vital components in the iron and steel industry, enabling power transmission, speed control, and torque conversion in various manufacturing processes. From rolling mills to continuous casting machines and material handling equipment, gears and gearboxes contribute to the efficiency, productivity, and quality of iron and steel production. As the industry continues to evolve, advancements in gear and gearbox technology will further enhance productivity, sustainability, and operational reliability, driving the future of the iron and steel industry towards more innovative and efficient practices.