
Worm Gear
Worm gears are a type of gear system commonly used in mechanical powertransmissions to achieve high gear reduction ratios. These gears consist of a worm, which is a cylindrical screw-like shaft, and a worm wheel, which is a gear with helicalteeth that mesh with the worm. In this blog post, we will explore the benefits andapplications of worm gears.
Advantages of Worm Gears
Applications of Worm Gears
Conclusion
Worm gears are a versatile and reliable type of gear system that can achieve high gearreduction ratios, are self-locking, and have a compact size. These features make themsuitable for a wide range of applications, including the automotive industry, materialhandling, food processing, and construction equipment. With their smooth operationand reliable performance, worm gears are an essential component of many mechanicalsystems.
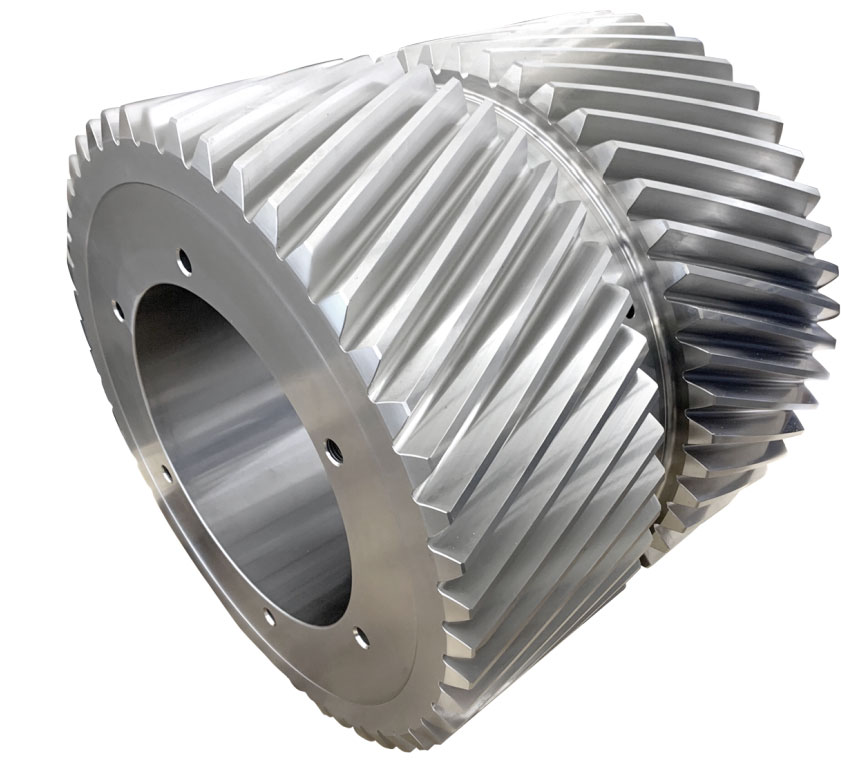
Double Helical Gears
Double helical gears, also known as herring bone gears, are a type of gear with two setsof helical teeth that are cut in opposite directions. This design eliminates the axial thrustthat is generated by helical gears with a single set of teeth, making them ideal for high-speed, high-torque applications where precise and reliable power transmission is critical.
How Do Double Helical Gears Work?
Double helical gears work by transmitting rotational power from one shaft to anotherthrough a series of interlocking teeth. Unlike helical gears with a single set of teeth, double helical gears have two sets of helical teeth that are cut in opposite directions. Thiscreates a V-shaped groove between the teeth that eliminates the axial thrust that is generated by single helical gears.
Advantages of Double Helical Gears
Applications of Double Helical Gears
Double helical gears are used in a variety of high-speed, high-torque applications, including:
Conclusion
Double helical gears are a critical component of many high-speed, high-torquemechanical power transmission systems. Their unique design provides severaladvantages over other types of gears, including reduced noise and vibration, increasedload capacity, improved precision, and greater efficiency. With their broad range of applications and benefits, double helical gears are an essential component of manymechanical systems that require precise and reliable power transmission.