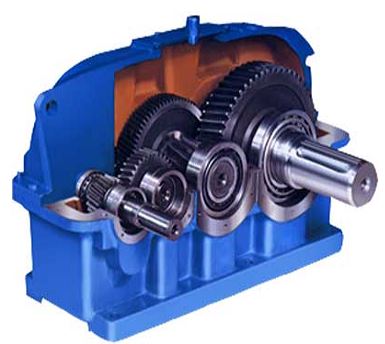
Gearbox Manufacturing Processes: From Design to Production
Gearboxes are critical components used in various industries, including automotive, aerospace, machinery, and robotics. They play a vital role in power transmission and motion control. The manufacturing of gearboxes requires a systematic approach to ensure precision, durability, and reliable performance. In this blog post, we will explore the key steps involved in gearbox manufacturing processes, from design to production.
Gearbox Design:
The first step in gearbox manufacturing is the design phase. Gearbox designers utilize computer-aided design (CAD) software to create detailed 3D models of the gearbox components, including the housing, shafts, bearings, and gears. The design process involves determining the gear ratio, torque requirements, input and output speeds, and the overall size and configuration of the gearbox.
Material Selection:
Selecting the appropriate materials for gearbox components is crucial for strength, durability, and performance. Common materials used for gearbox manufacturing include alloy steels, cast iron, aluminum alloys, and various engineering plastics. The material selection is based on factors such as load capacity, operating conditions, temperature, and cost considerations.
Machining and Fabrication:
After the gearbox design is finalized, the manufacturing process begins with machining and fabrication of the gearbox components. This involves processes such as milling, turning, drilling, and grinding to shape the gearbox housing, shafts, and other parts. CNC (Computer Numerical Control) machines are often used to ensure accuracy and consistency in the manufacturing process.
Gear Cutting:
Gear cutting is a critical step in gearbox manufacturing. It involves the production of gears with the desired tooth profiles and specifications. Gear cutting methods such as hobbing, shaping, milling, or broaching are employed to create the gears. The gear cutting process ensures proper gear meshing and efficient power transmission within the gearbox.
Assembly and Fitting:
Once the gearbox components, including the housing, shafts, bearings, and gears, are manufactured, they are assembled and fitted together. This involves precise alignment and fitting of the components to ensure smooth operation and accurate gear meshing. Lubrication systems and seals are also installed during the assembly process to provide proper lubrication and prevent contamination.
Testing and Quality Control:
Gearboxes undergo rigorous testing and quality control measures to ensure their performance and reliability. Functional tests, such as load testing, vibration testing, and endurance testing, are conducted to verify the gearbox’s ability to handle the specified loads and operating conditions. Additionally, quality control inspections, including dimensional checks and surface finish evaluations, are performed to ensure adherence to design specifications and standards.
Final Finishing and Packaging:
After testing and quality control, the gearbox undergoes any required final finishing operations, such as deburring or surface treatment, to improve its appearance and functionality. The gearbox is then properly packaged, ensuring protection during transportation and storage until it reaches the end-user or assembly line.
Gearbox manufacturing is a complex process that requires precision and attention to detail. From gearbox design and material selection to machining, gear cutting, assembly, testing, and final finishing, each step plays a vital role in producing a high-quality and reliable gearbox. By following stringent manufacturing processes and adhering to quality control measures, gearbox manufacturers can deliver products that meet the performance requirements and specifications of various industries.